A Complete Guide to Silicone Rubber
What is Silicone Rubber?
Silicone rubber is a popular high-temperature synthetic elastomer used for various applications within most industry sectors. Due to its excellent temperature resistance, FDA approval and non-toxicity properties, Silicone is the preferred rubber compound for manufacturing products for the medical and food industry. However, with superb general resistance to most substances, Silicone rubber seals can be used within almost every industry sector for most applications. With a heavy reliance on synthetic rubber compounds, Silicone has taken its place as one of the most common and widely used raw materials for manufacturing seals and associated products. Silicone can be extruded in a range of hardnesses and densities in solid or closed-cell materials.
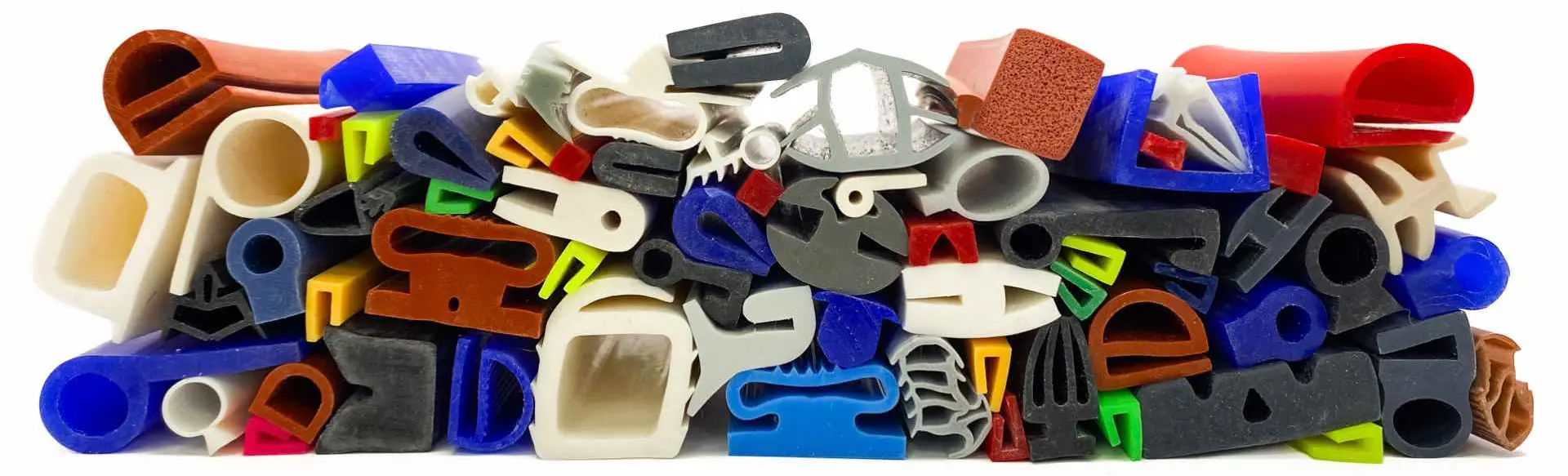
Learn about the history of Silicone, how the compound is created, and the benefits of using it to manufacture bespoke extrusions and cut rubber strip.
How is Silicone Rubber Made?
In the search for better insulating materials for motors and generators, research by scientists at Corning Glass Works and General Electric identified that synthesising silicone polymers created a reliable heat resistant material that performed better than resin-impregnated glass fibres. Continuing their research to further understand the unique properties of Silicone, General Electric opened its own manufacturing plant to commercially produce and supply various Silicone rubber compounds.
The process used by General Electric to create these compounds involves heating the chemical element silicon to 1800°C, adding methyl chloride and distilling. To this day, the basic principles to create Silicone still follow the same stages first identified by General Electric. The end result is a Silicone rubber compound that can be used to create extruded profiles, moulded gaskets or flat sheets of rubber.
Extruded profiles are manufactured using an extruder that pushes the rubber compound through an extrusion tool (known as a die). This process uses pressure and temperature to create the required shape which is then cured and hardened using a vulcanising line, steam line, salt bath or autoclave cure. Silicone rubber can also be rolled to a desired thickness using a calender roller. This process creates large sheets of rubber that can be cut into narrow strips for edging or cushioning applications.
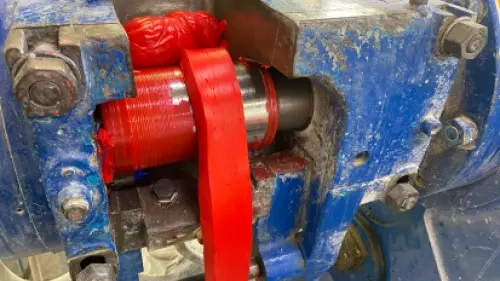
Although the Silicone rubber compound is initially semi-solid, it can be extruded into both solid rubber and expanded sponge rubber products. Nucleating agents, such as nitrogen and carbon dioxide, are added to the compound during the extrusion process to create a sponge-like cellular structure that can be used to make a watertight seal to stop water ingress. It is possible to achieve different hardnesses and densities by adjusting the gas injection rate.
Advantages of Silicone Rubber
Silicone is a versatile general purpose material that can be used for a diverse range of applications that cannot be achieved with other rubber compounds. With a unique set of properties, Silicone is often the preferred material for projects requiring a high-temperature and long lasting sealing solution. Some of the key characteristics and properties of Silicone rubber include;
- Temperature
Resistance: Operating within a temperature range between -60°C and 230°C,
seals manufactured from Silicone rubber can withstand extremely low and high
temperatures. Remaining flexible below freezing, Silicone is well-suited for
applications in cold climates and cryogenic environments. It can also withstand
elevated temperatures up to approximately 230°C without significant degradation
of its physical properties. This makes it suitable for use in exceptionally high-temperature environments, such as automotive engine components, ovens and
industrial applications.
- Weathering:
Similar to most other synthetic rubber compounds, Silicone can withstand
exposure to the elements making it suitable for seals manufactured for outdoor
environments. It exhibits good resistance to UV and ozone, which helps maintain
its physical properties and colour when used outdoors for extended periods of
time. Rubber seals manufactured from Silicone also demonstrate outstanding
water resistance and are impermeable to moisture.
- Chemical
Resistance: Silicone rubber is resistant to a wide range of chemicals,
including acids, solvents and other common industrial chemicals. The material
can withstand exposure and contact with many corrosive substances without
significant degradation.
- Food Safe: Silicone extrusions can be manufactured from metal detectable and FDA approved materials that are considered safe for contact with food. As food safe Silicone is biocompatible and non-toxic, it can also be used in medical devices, implants and prosthetics.
In addition to being a material suitable for use in food factories and extreme temperature environments, Silicone exhibits other properties that make it an ideal material for most sealing applications. These properties include;
- Flexibility
and Elasticity: Silicone is a highly flexible and elastic rubber compound
that can stretch or compress and return to its original shape without permanent
deformation. This is a useful characteristic for sealing applications where the
section will be compressed to create a reliable watertight seal.
- Low
Production Runs: Although Silicone extrusions are more expensive to produce
than those manufactured in other synthetic compounds, the minimum production
run is often significantly lower. This helps reduce the overall price for the
extrusion in situations where you only require a small quantity. As Silicone
rubber is known for its durability and resistance to aging, seals manufactured
in this material also need to be less frequently replaced so offers an ongoing
cost saving.
- Closed-Cell:
Gases can be injected into the rubber compound during the extrusion process
to make a compressible sponge. This is a closed-cell material that does not
absorb water and can be used to create watertight seals on hatches, doors and
lockers. In the same way as other closed-cell products, Silicone sponge seals
can be extruded into almost any shape in any size with fine details.
- Colours
Matching: It is possible to manufacture custom Silicone sections to any
colour specification. The compound is pigmented during the manufacturing
process to match the colour of an existing seal or RAL colour number. This is
particularly useful for instances where you need an extrusion that matches your
companies branding, or are required to use a colour that can be easily identified
in food and drink manufacturing environments.
- Metal Detectable: As Silicone is commonly used within food processing and manufacturing environments, it is possible to extrude Silicone rubber seals in metal detectable grades. This type of rubber contains metal particles or additives that allow machines using metal detectors to identify failed seals and trims that breakdown and enter the food supply. This is essential for industries where contamination control is crucial.
Disadvantages of Silicone Rubber
Although Silicone rubber has many advantages, such as its high-temperature resistance and flexibility, it also has some disadvantages that make it unsuitable for specific applications. Some of these disadvantages include;
- Fuel and Oil
Resistance: Silicone rubber exhibits moderate resistance to occasional or
short-term exposure to fuels and oils under certain conditions and
temperatures. However, constant contact with these substances under the wrong circumstances
will cause the rubber to swell and deteriorate. For applications that require a
rubber compound suitable for contact with fuels and oil, we recommend using
Nitrile or Viton which offer an excellent resistance to these substances.
- Poor
Adhesion: As Silicone rubber has a naturally non-stick surface, it can be
difficult to bond to other materials. Silicone sealants or special primers are
the only adhesives that can achieve adequate adhesion and bond Silicone based products to other substrates. This can limit the use of Silicone
extrusions to applications that do not require very strong adhesion.
- Poor Tear and Abrasion Resistance: Seals manufactured from Silicone have a relatively low tear strength compared to other elastomers, such as EPDM and Neoprene. This makes the material less suitable for applications where the seal will be fitted in environments that could cause it to tear or puncture. Silicone also offers poor abrasion resistance.
Common Applications and Uses
Silicone rubber is an incredibly versatile compound known for its unique combination of properties that make it suitable for a wide range of applications across most industries. These products can be manufactured to order from both solid Silicone and expanded Silicone to suit the desired application. Although it is best to select a rubber compound based on the substances it will come into contact with, Silicone is a superb material with excellent all-round properties. Silicone sealing solutions are commonly supplied to the following industry sectors for use on their projects and products.
Industries
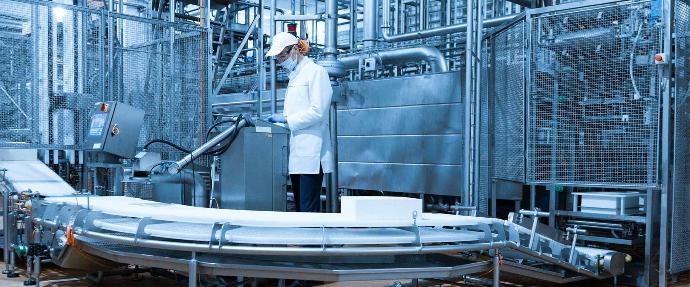
Food Manufacturing
Silicone is the most common rubber material supplied to the food and dairy industry. Seals used in this environment need to be manufactured from materials approved by the US Food and Drug Administration. FDA-approved Silicone is considered safe for contact with food and conforms to the health and safety requirements associated with food manufacturing. We commonly extrude Silicone rubber seals with a blue pigmentation as this is a colour that can be easily identified in the food chain.
The food industry also utilises metal detectable grades of
Silicone. These materials contain tiny metal particles that can be identified
if parts of a failed seal break down and enter the food supply.
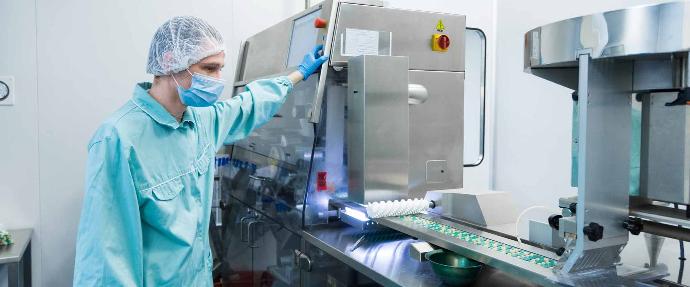
Medical, Pharmaceutical & Healthcare
Due to the non-toxic properties of Silicone, seals manufactured for medical and pharmaceutical applications are usually extruded from FDA and USP certified Silicone compounds. These sections are used for sealing applications and edge protection on medical equipment, such as clean rooms and defibrillators. As Silicone is known for its biocompatibility, it is well-tolerated by the human body when in contact with bodily tissues. Silicone also remains stable at low and high temperatures, which allows Silicone extrusions on equipment to be sterilised without the risk of degrading.
However, depending on the specific medical application, seals supplied to this industry can be manufactured from almost any material that has a good resistance to cleaning chemicals. This includes EPDM, Neoprene, PVC and Silicone.
Types and Grades of Silicone Rubber
Silicone rubber is available in a selection of types and grades that can be used in most industry sectors. Each variant offers different properties, characteristics and benefits that make it possible to select the correct Silicone compound most suitable to the required application. Our range includes materials suitable for contact with food in food factories, high temperature environments or low-quantity prototyping. Silicone can be cut from sheet or extruded in sponge and solid compounds to create trims suitable for edge protection or sections that can be used to create a watertight seal.
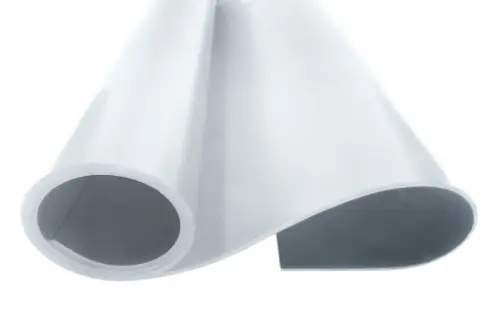
General Purpose Silicone Rubber
Our general purpose Silicone rubber is suitable for most sealing applications. This is a standard grade that offers all of the properties of Silicone including a good resistance to most substances and stability when used in extreme temperatures. It can be supplied as cut lengths or extruded to create bespoke seals and trims in a range of hardnesses from 20°sh A to 80°sh A. It is also FDA compliant to 21 CFR 177.2600 and WRc approved to M103580/A-H.
Material Data Sheets
20 Shore A
30 Shore A
40 Shore A
50 Shore A
60 Shore A
70 Shore A
80 Shore A
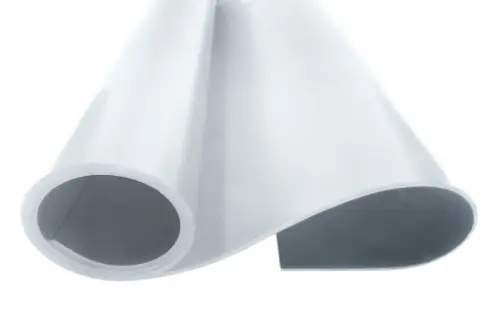
FDA Approved Silicone Rubber
FDA approved silicone is compliant to 21 CFR 177.2600 and WRc approved to M103580/A-H. This is a standard grade that meets stringent FDA standards for safety and purity. It is commonly used within healthcare, food processing and pharmaceuticals. It can be supplied as cut lengths or extruded to create bespoke seals and trims in a range of hardnesses from 20°sh A to 80°sh A.
Material Data Sheets
20 Shore A
30 Shore A
40 Shore A
50 Shore A
60 Shore A
70 Shore A
80 Shore A
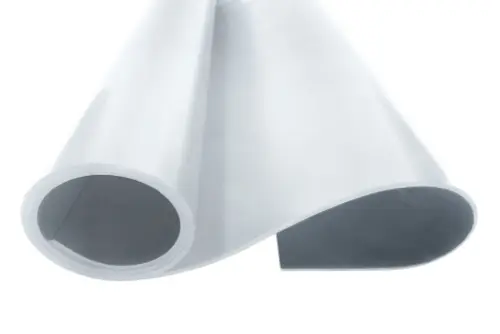
High Tear Strength Silicone Rubber
General purpose silicone can tear or puncture when subjected to stress or contact with a sharp object. Our high tear strength silicone is formulated to have a higher elongation and tear strength that these general purpose compounds. It can be extruded into custom rubber seals with a hardness between 50°sh A to 70°sh A.
Material Data Sheets
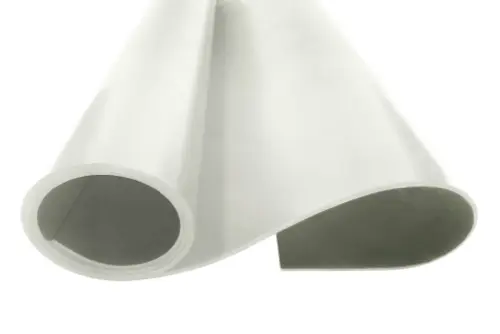
High Temperature Silicone Rubber
Unlike most other Silicone compounds that start to degrade if subjected to temperatures above 230°C, a high temperature Silicone rubber compound can be used in extremely high temperatures up to 300°C. It is FDA compliant to 21 CFR 177.2600 and can be extruded in a range of hardnesses between 20°sh A and 80°sh A.
Available Compounds
20 Shore A
30 Shore A
40 Shore A
50 Shore A
60 Shore A
70 Shore A
80 Shore A
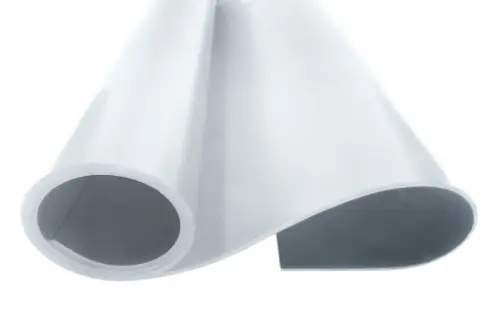
Heat Stabilised Silicone Rubber
Heat stablished silicone is a general purpose compound that contains an additional additive that increases the heat stability to an extended temperature range between -50ᵒC to +260ᵒC. Rubber sealing products manufactured from this material are available with a hardness between 30°sh A to 80°sh A.
Available Compounds
20 Shore A
30 Shore A
40 Shore A
50 Shore A
60 Shore A
70 Shore A
80 Shore A
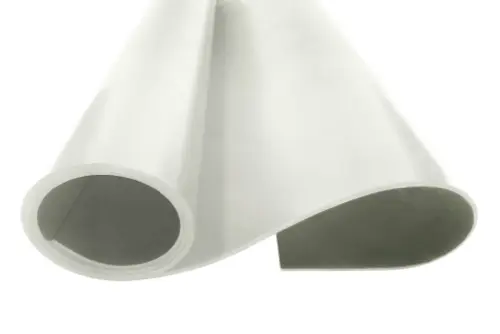
Flame Retardant Silicone Rubber (Aerospace Specification)
Our flame retardant silicone rubber is an aerospace specification that is designed for extreme aerospace conditions. It offers excellent fire resistance, low smoke and low toxicity, meeting strict aviation safety standards. Used for products that requires thermal stability in high-temperature and high-altitude environments.
Available Compounds
20 Shore A
30 Shore A
40 Shore A
50 Shore A
60 Shore A
70 Shore A
80 Shore A
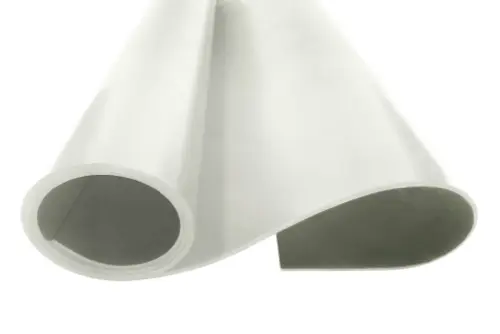
Flame Retardant Silicone Rubber (Rail Specification)
This flame retardant silicone is a specialised rail specification grade that is designed for rail and transportation industries. It meets stringent safety standards, offering low smoke, low toxicity and self-extinguishing properties. Ideal for seals, gaskets, and insulation, it enhances passenger safety by preventing fire spread in high-risk environments.
Available Compounds
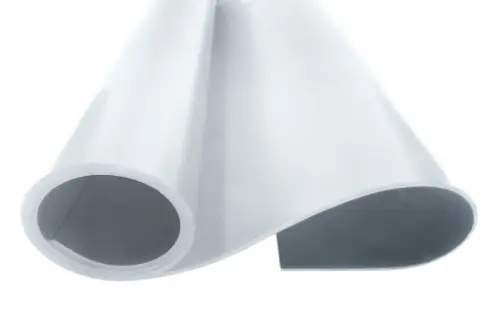
Steam Resistant Silicone Rubber
Unlike other rubber compounds, silicone performs well in steam filled environments. Products manufactured from steam resistant silicone operate well in high temperatures, hot air and pressure. This material is only available in one hardness (70°sh A) but has generally good all round properties, tensile strength and rebound resilence.
Available Compounds
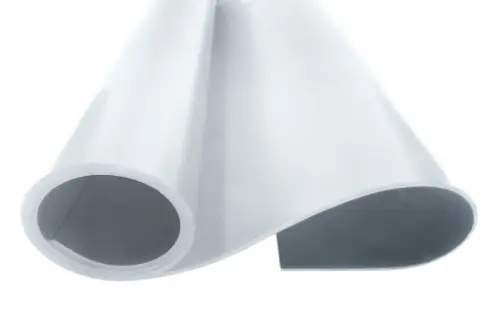
Inflatable Grade Silicone Rubber
Inflatable seals are commonly manufactured from a special grade of Silicone rubber. This material demonstrates different characteristics, such as higher tear strength and excellent joining properties. It is available in 60°sh.
Available Compounds
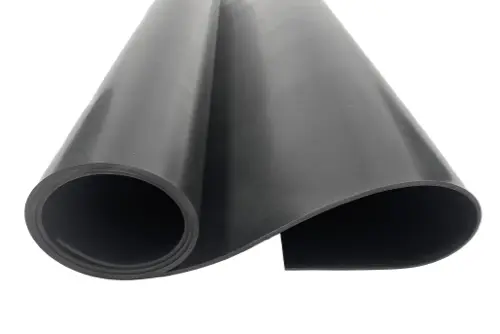
Conductive Silicone Rubber
Conduction silicone is an electro-conduction platinum cured silicone rubber. This material has a low volume resistivity after high temperature exposure. Due to the compounding process required to formulate this compound, it is only available in black with a hardness of 75°sh.
Available Compounds
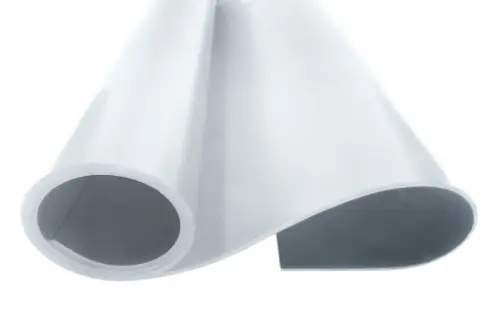
Metal Detectable Silicone Rubber
Silicone extrusions can also be manufactured from a peroxide cured metal detectable Silicone rubber compound. This material offers the same properties as Silicone but contains metal powder so can be identified with metal detectors. It is commonly used in machines to help with the identification of foreign objects. This grade of Silicone is compliant to FDA 21 CFR 177.2600 and BfR chapter XV.
Available Compounds
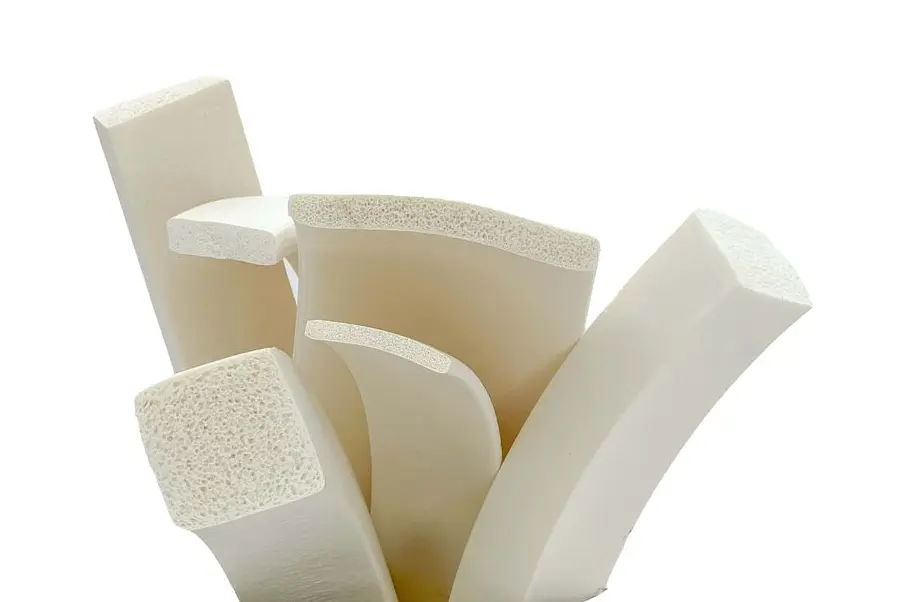
Sponge Silicone Rubber
General purpose silicone is also available as a closed-cell sponge that can be used to create watertight seals to stop water ingress. This material offers minimal water absorption (IP65-66 achievable) and is FDA approved so is suitable for contact with food. Silicone sponge rubber can be extruded in a range of densities between 10 lb/ft and 33 lb/ft. This material compound is RoHS compliant.
Available Compounds
35 Shore OO
42 Shore OO
55 Shore OO
65 Shore OO
70 Shore OO
80 Shore OO
Contact Us
With over 50 years' experience in the rubber sealing industry, our team has extensive experience in finding sealing solutions for our customers. Contact our experts via phone or email for sealing advice or bespoke quotations.
Email:
sales@sealsplusdirect.co.uk
Telephone:
01425 617722