Rubber Materials
Seals Direct offer an extensive range of natural rubbers, silicone rubbers, synthetic rubbers and plastics suitable for different temperatures, chemicals and compression strengths. The majority of these rubber materials are supplied as extruded profiles, moulded gaskets, or cut strip and sheet form.
Rubber is an excellent multi-functional and hard wearing material that can be extruded, moulded and cut into an endless variety of shapes. With over 40 types of rubber and plastic compounds available, it is possible to select the type most suitable for the required application. Different industry sectors have different demands and manufacturing your extrusion or gasket in the correct material is essential for providing a long lasting sealing solution.
Different Rubber Materials
For many years, rubber was only available in natural forms harvested from trees and plants. Over the last century, man-made rubber compounds such as EPDM, Neoprene and Nitrile were developed by vulcanising and experimenting with petroleum by-products. Although there are over 40 different types of rubber compounds, they can all be categorised within three different areas; natural rubber, synthetic rubber and silicone.
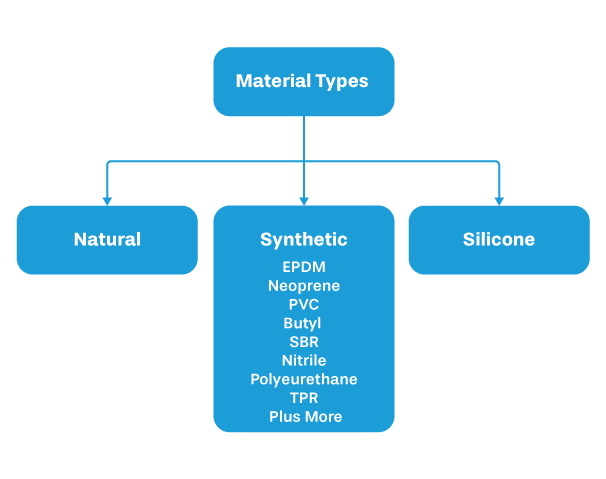
What is Natural Rubber?
Natural rubber is made by extracting latex from trees and some plants. There are over 2,000 different types of tree that produce latex, but the Hevea brasiliensis tree which can grow over 43 metres tall, is the most common. Latex is obtained by tapping the tree by making a cut in the bark and harvesting the liquid sap. This is then processed into a usable natural rubber compound which can be used for extruded seals and rubber strips.
Natural rubber is an excellent material for applications that require high elasticity and tensile strength. It has great compression recovery so can reliably be used for seals with large closing and compression forces. Unfortunately, due to the way natural rubber is manufactured, it is often more expensive compared to synthetic alternatives. It is also recommended that natural rubber seals are installed in environments that are not subjected to excessive amounts of UV radiation. Natural rubber is not UV stable so will start to degrade, lose elasticity and form cracks if used in natural light environments.
What is Synthetic Rubber and Plastic?
Unlike natural rubber, synthetic rubber does not occur naturally and is man-made using petroleum by-products. The procedure to manufacture a synthetic rubber compound follows a very similar process differing ever so slightly for the particular type of material. The production process combines a hydrocarbon mixture with natural gasses. This process produces monomers which bind together to create polymers before being formed into a rubber compound through the addition of chemical agents. These rubber compounds can then be used to create rubber seals and extrusions.
Synthetic rubbers copy most of the properties of natural rubber but can be used with higher temperatures and are often oil and chemical resistant. The large amount of synthetic rubbers available makes it easy to find a material suitable for the desired application. Whether that is resistance to petroleum based oils and fuels, extreme temperatures or weathering. Most synthetic rubbers are available in either sponge or solid forms, and can be supplied as extruded profiles, moulded gaskets, or cut into strips and sheet.
What is Silicone?
Silicone rubber, being a synthetic polymer made from silicon, sits outside of its natural and synthetic rubber counterparts. Silicon is the raw chemical element which when heated to 1800°c, combined with methyl chloride and distilled forms a raw silicone compound. This compound can then be used for making extrusions, sealants or lubricants.
Silicone rubber can be supplied as extruded profiles, moulded gaskets, or cut in strips and sheets. It is an excellent material for applications that require a good compression set or will be subjected to extreme environments and temperatures between -55 °C and 300 °C. Silicone can also be pigmented to virtually any RAL colour so is often the material of choice for rubber seals that will be used in food safe environments, need to match your company's branding or be a vibrant colour for hazard identification. The main disadvantage of silicone is that it has poor abrasion resistance and can tear if it comes into contact with a sharp object
Rubber Material Selection
It is important to select a rubber material that suits the required application. Different rubbers are required for different purposes and selecting the right material is essential to avoid the seal degrading over prolonged use. Each industry sector has different demands and the final product may need to be installed in areas that may cause the seal to be subjected to oil, fuel, chemicals or extreme temperatures. Choosing the right rubber material will ensure you have a long lasting sealing solution.
It is also essential to choose the correct material hardness and density to ensure that the seal compresses without the risk of compression set. Using a material that is hard with low closing forces will create an area difficult to seal, whereas using a softer seal may squash and fail if compressed too much.
If you require guidance in choosing the best material for your application, please contact us with your requirements.
Rubber Material Types
Elastomers come in many different grades and are used extensively in a wide range of industrial and domestic applications. With over 50 years of experience in the rubber sealing industry, Seals Direct has developed long-standing relationships with rubber compounders. We have access to over 40 different types of rubber and plastic compounds and are happy to provide advice on the most suitable material for your application. The majority of our rubber materials are available in sponge or solid forms and can be supplied as extruded profiles, gaskets or cut in sheet or strip form.
Sponge Rubber
Expanded
closed-cell sponge rubber is ideal for sealing applications with low
compression forces. They can be used to create watertight seals to stop water
ingress.
Solid Rubber
Solid
rubber can be used for sealing and edging applications within most industry
sectors. It can be cut into strip, supplied as large sheets or manufactured
into complex gaskets.
Products made from sponge or solid rubber can be manufactured from a wide variety of materials. This selection allows you to choose a suitable compound that allows for any environmental, chemical or temperature demands of the required application.
Ethylene Propylene Diene Monomer (EPDM)
EPDM
is a versatile rubber with an excellent resistance to weathering, ozone and
chemicals. It is able to withstand low and high temperature ranges without
deforming.
Natural Rubber (NR)
Natural
rubber has a high tensile strength and excellent resistance to cutting, tearing
and compression. However, it is not UV stable and only has a moderate
resistance to temperature.
Neoprene Rubber (CR)
Neoprene
is available as a sponge or solid and is a good general purpose rubber with
moderate resistance to oils and UV. It is often used in applications where
other materials would fail.
Nitrile Rubber (NBR)
Nitrile
has an excellent resistance to petroleum based oils, fuels, silicone greases
and hydraulic fluids. It also has a good resistance to temperature and
generally good mechanical properties.
Styrene-Butadiene Rubber
(SBR)
This
general purpose synthetic rubber is often used as a cost effective alternative
to natural rubber. Similarly to natural rubbers, it has a high abrasion
resistance and compression set. It is not suitable for contact with chemicals
or UV.
Silicone Rubber (SIL)
Silicone
is suitable for both low and high temperature ranges and is ideal for static
applications due to its poor tear resistance and tensile strength. Silicone can
be pigmented with any RAL colour.
PVC
PVC
is one of the most common plastics and can be supplied in various rigid, soft
or flexible forms. It has good resistance to chemicals and is relatively
inexpensive to manufacture.
Viton
Viton
has an excellent chemical resistance and very good temperature range. It is
used in a diverse range of applications where a high-quality sealing solution
is required.
ISO 9001:2015 Certified
BSI Certificate Number: FS 807117
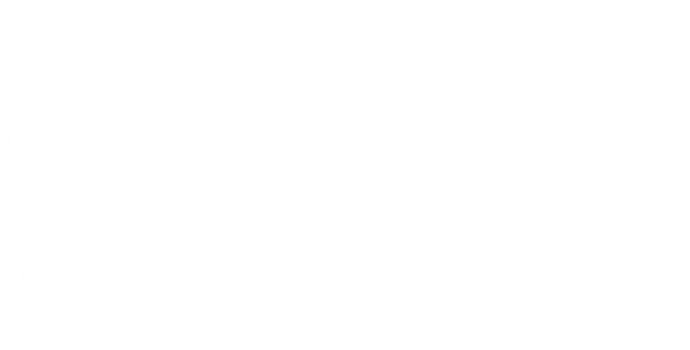
Contact Us
With over 50 years' experience in the rubber sealing industry, our team has extensive experience in finding sealing solutions for our customers. Contact our experts via phone or email for sealing advice or bespoke quotations.
Email:
sales@sealsplusdirect.co.uk
Telephone:
01425 617722