A Complete Guide to Nitrile Rubber
What is Nitrile Rubber?
Nitrile rubber, also known as Buna-N or NBR, is an oil and fuel resistant synthetic rubber. Its properties make it suitable for manufacturing rubber products that will come into contact with oils, fuels, alcohols, hydraulic fluids and chemicals. Nitrile also exhibits excellent tensile strength and abrasion resistance.
With an annual production that exceeds 36 million metric tons, Nitrile is expected to continue to gain popularity due to an increase in the demand for synthetic rubbers within the automotive, engineering and industrial industry sectors. It can be cut into strips from large sheets or extruded to create bespoke sealing solutions. These products can be manufactured using solid nitrile or a closed-cell sponge in a range of hardnesses and densities.
This guide provides a detailed explanation of the history of nitrile rubber and discusses the advantages and disadvantages of using this material for manufacturing rubber extrusions.
How is Nitrile Rubber Made?
The development of synthetic rubber became a significant focus in the early 1900s, due to the increased demand of rubber materials during World War 1. Researchers were looking for alternatives to natural rubber which was in short supply and unsuitable for prolonged use in outdoor environments. The first significant step towards the development of nitrile rubber occurred in the 1920s when chemists began experimenting with butadiene and acrylonitrile monomers. This copolymer had a good oil resistance that offered a significant improvement for many industrial applications.
The process used to create nitrile rubber involves emulsifying butadiene and acrylonitrile in water then polymerising the result. The ratio of these two products is often adjusted to suit the required characteristics, such as the flexibility of the extrusion or its resistance to oil or fuel. To this day, the process used to manufacture nitrile compounds follow the same basic stages identified during the early 1900s. The end result is a strong and durable rubber with excellent resistance properties that can be used to manufacture bespoke extrusions, moulded gaskets or flat strips of rubber.
Nitrile rubber extrusions are manufactured to order in a variety of forms. Using a machine called an extruder, the rubber compound is pushed through an extrusion tool (known as a die) to create the required shape. This machine uses pressure and temperature to extrude continuous lengths of a profile that is then cured and hardened using vulcanising line, steam line, salt bath or autoclave cure. Nitrile rubber can also be manufactured as flat sheets of rubber for edging or cushioning applications. These sheets are rolled using a calender roller that squashes the rubber compound to the desired thickness. This sheet can then be used to create cut rubber strips or bespoke gaskets.
Rubber compounds are initially a semi-soild but can be converted into solid rubber or expanded sponge rubber products during the manufacturing process. By adding nucleating agents, such as nitrogen or carbon dioxide, it is possible to create a cellular structure suitable for manufacturing compressible closed-cell sponge seals to help stop water ingress. Adjusting the speed at which these nucleating agents are added to the compound helps achieve different hardnesses and densities.
Advantages of Nitrile Rubber
There are many advantages for using nitrile rubber for bespoke extrusions and gaskets. As a compound with exceptional resistance to most fluids, nitrile is a reliable material commonly used across various industry sectors. Some of the key benefits of using nitrile include;
- Oil and
Fuel Resistance: The most sought after benefit of nitrile rubber is its
resistance to oils, fuels and petroleum-based fluids. As a material that does
not easily swell or degrade, nitrile provides a long-lasting and reliable
choice for applications involving contact with these substances. Nitrile is
hydrophobic, which means that it repels water allowing it to resist the
penetration of oil and water-based liquids. The level of oil resistance depends
on the amount of acrylonitrile in the rubber compound. A higher ratio makes the
rubber less resistant to swelling from oil contact, but results in the seal
becoming slightly stiffer at lower temperatures.
- Chemical
Resistance: Although harsh chemicals will cause most rubber compounds to
breakdown and degrade, nitrile performs well against a broad spectrum of
chemicals, including acids and solvents.
The nitrile rubber market is expected to reach $4.6 billion by 2028, with an annual growth rate of 4.8% between 2022 and 2028.
As well as demonstrating an excellent resistance to most fluids, products made from nitrile also display exceptional functional properties that further expand their application within the automotive and engineering industry sectors. These properties include;
- Durability:
NBR rubber is known for its durability, long service life and abrasion
resistance. Together with its ability to withstand oil and fuel, nitrile is
suitable for tough and dirty industrial applications such as conveyor belts, o
rings and engine hoses. Seals manufactured from nitrile also demonstrate good
flexibility and are unlikely to be stretched during installation.
- Temperature
Resistance: Nitrile can effectively operate within a moderate temperature
range between -40°C and 120°C. Although there are other materials such as
Silicone more suitable for high temperature applications, these materials have
a poor resistance to oil and fuel. These characteristics make nitrile one of
the best and affordable oil resistant rubber compounds suitable for use within
a modest temperature range.
- Water
Resistance: As either a solid or closed-cell sponge, nitrile rubber can
withstand short-term exposure to water and is suitable for applications where
exposure to moisture is a concern. However, pro-longed or continuous exposure to
water may lead to swelling, softening and reduce the rubbers mechanical
properties.
- Compression
Set: NBR exhibits a good resistance to compression set. Seals manufactured
from nitrile maintain their shape and sealing properties after prolonged
compression.
- Hybrid Compounds: It is possible to blend nitrile with other expanded materials, such as PVC, to make hybrid compounds with increased oil resistance at a lower cost. By itself PVC should not come into contact with large amounts of oil. However, combining this material with expanded nitrile creates a hybrid material at a significantly lower cost with a fair resistance to substances that would normally cause PVC to degrade.
Disadvantages of Nitrile Rubber
Although nitrile rubber has many advantages within the automotive and engineering industry, there are occasions where it is unsuitable for some applications. In this instance it is sometimes worth considering alternative materials such as EPDM, Silicone or Viton. Some of the disadvantages of NBR rubber include;
- Ozone and
UV Stability: Nitrile is susceptible to damage from ozone and ultraviolet
radiation which can cause cracking and degradation. Seals manufactured from
nitrile are not well suited for outdoor applications that will experience
prolonged exposure to sunlight. In such cases, other rubber materials such as
EPDM, Silicone or Viton, with better UV resistance may be more suitable.
- Cost: Applications that do not require a rubber material resistant to oils and fuels, would be better suited with a lower cost compound such as EPDM or Silicone. However, in comparison to other oil and fuel resistant materials such as Viton, nitrile offers an affordable alternative. The minimum order quantity for a bespoke nitrile extrusion is around 100 metres, depending on the size and complexity of the profile.
Common Applications and Uses
Nitrile rubber is a durable compound known for a unique set of characteristics that make it the preferred compound for applications across automotive, engineering and industrial industry sectors. Although it is best to select a rubber compound by considering the specific requirements of the application, nitrile is an ideal material with excellent resistance properties for most indoor uses. NBR is commonly supplied to the following industry sectors as extruded sections, cut gaskets or strip and sheet.
Industries
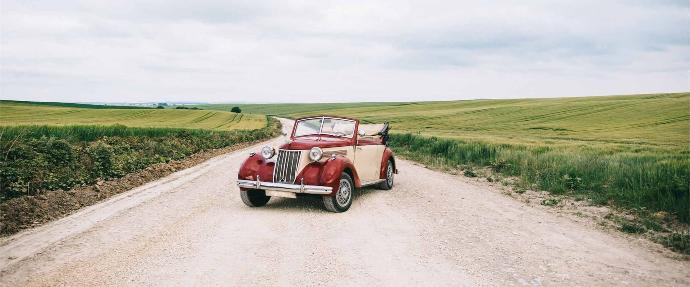
Automotive
Nitrile is one of the preferred materials for seals, gaskets and o rings manufactured for automotive applications. Although a lot of these products are being replaced with EPDM alternatives, nitrile rubber is still used to manufacture seals that will be fitted in areas that may come into contact with oil, fuel and hydraulic fluids. This includes engine enclosures, fuel tanks, oil systems, transmission belts and suspension components.
As a material that absorbs shock and vibrations, nitrile is a suitable material for use on vehicles where the seal will be subjected to vibrations originating from the engine and road.
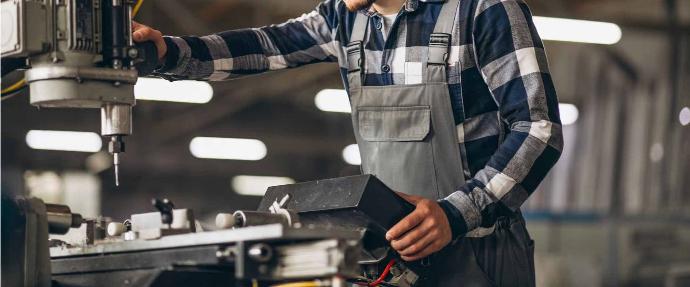
Engineering and Industrial
Nitrile rubber is commonly used within various engineering and industrial environments due to its resistance to a wide range of industrial fluids, such as oil, fuel and chemicals. These properties are valuable in industrial machinery and equipment that rely on hydraulic systems, lubrication and fuel handling. The chemical resistance of NBR rubber also makes it suitable for applications in chemical processing and manufacturing laboratories that require long lasting sealing solutions.
As a good all-round industrial material, the durability and abrasion resistance of nitrile rubber seals allow them to withstand dynamic movements, vibrations and abrasive surfaces on industrial machinery.
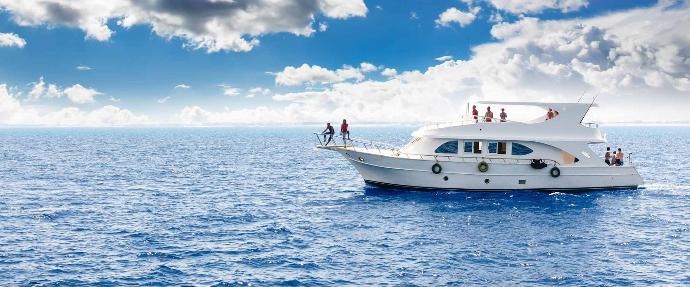
Marine
Seals manufactured from nitrile can be used in certain marine environments depending on the specific conditions and application. NBR has some desirable properties for marine use, such as oil and fuel resistance, so is an ideal material for rubber products that will be fitted in or near engine systems, hydraulic systems or fuel handling equipment.
However, nitrile has several limitations that may cause the material to degrade and breakdown if incorrectly used in marine environments. Although nitrile offers a good resistance to water exposure, it is not suitable for prolonged water immersion or exposure. Nitrile is also not as resistant to UV and weathering as some other elastomers, such as EPDM.
Types and Grades of Nitrile Rubber
Nitrile rubber is available in a selection of grades and hardnesses to suit different applications. As a material that can be extruded or cut from sheet and manufactured in both sponge and solid variants, nitrile offers a solution to most sealing applications. The formulation and hardness of nitrile can vary, so selecting the correct grade is essential for optimal performance within a particular environment.
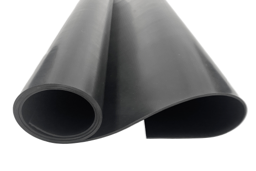
Commercial Grade Nitrile Rubber
Commercial grade nitrile rubber is a general purpose product that offers all of the properties of nitrile, including a good resistance to oil, fuel and most other substances. It is available in a range of hardnesses between 60°sh A to 70°sh A.
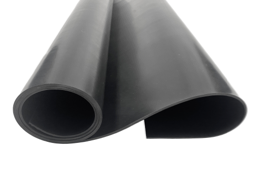
Nitrile Rubber to British Standard BS2751
Nitrile is also available in a grade compliant
with British Standard BS2751 specifications. This compound uses a higher
concentrate of acrylonitrile
to improve its mechanical properties and resistance to oil and fuel. It is
available in a selection of Shore A hardnesses between BA40 to BA70.
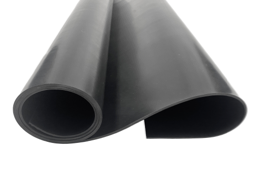
Solid Nitrile Insertion Rubber
Insertion rubber is manufactured from commercial
grade nitrile but contains a mesh reinforcement layer. This layer, known as the
insertion, runs through the centre of the material to increase its strength and
minimises the chance of the material being stretched. This material is
available in a selection of hardnesses, similar to commercial grade sheeting.
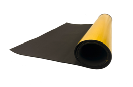
Expanded Nitrile / PVC Closed-Cell Sponge Rubber
Nitrile
sponge is also available as a closed-cell sponge that can be used to create
watertight seals to stop water ingress. Expanded nitrile is often blended with
expanded PVC to reduce the production cost but still offer some oil and fuel
resistance. This material can be used as a thermal insulator.
Contact Us
With over 50 years' experience in the rubber sealing industry, our team has extensive experience in finding sealing solutions for our customers. Contact our experts via phone or email for sealing advice or bespoke quotations.
Email:
sales@sealsplusdirect.co.uk
Telephone:
01425 617722