A Complete Guide to High Temperature Silicone Rubber
What is High Temperature Silicone Rubber?
High temperature silicone rubber is a variant of silicone formulated to retain its physical properties and performance in extreme temperature environments. It is a general purpose compound capable of withstanding temperatures ranging from -50°C to as high as 300°C. This material is valued for its stability, resistance to thermal degradation and flexibility under varying conditions.
Silicone rubber’s unique properties stem from its polymer structure, which consists of alternating silicon and oxygen atoms. This structure provides inherent thermal stability and chemical resistance, making it a go-to choice for applications where traditional rubbers fail. It is also an electrical insulator and can be formulated to meet food-grade and medical-grade standards.
Appearance
Initially off-white but can be pigmented to red oxide or grey.
Tear Strength
Resistance to tearing between 23N/mm and 36N/mm.
Density
Formulated for a density at 20ᵒC of around 1.15 g/cm3.
Hardness
Available between 24ᵒ Shore A and 79ᵒ Shore A.
Tensile Strength
Tensile strength between 9.0g/cm3 and 11.0g/cm3.
Elongation at Break
Flexibility between 420% and 920% without breaking.
Temperature Range
Operates
effectively between -50°C and 300°C.
Rebound Resilience
Recovery from deformation between 42% and 57%.
Learn how high temperature silicone is formulated, its benefits over general purpose silicone and common applications within the industry.
How is High Temperature Silicone Rubber Made?
The production of high temperature silicone rubber starts with the preparation of raw materials. Silicon, a key component, is derived from silica sand and combined with hydrocarbons obtained from petroleum or natural gas. These materials are processed to produce chlorosilanes, which serve as the base chemicals for silicone production. The chlorosilanes are then hydrolyzed to form silanols, which undergo condensation reactions to create polydimethylsiloxane (PDMS) chains. These chains form the backbone of silicone rubber.
To enhance the mechanical and thermal properties of the material, reinforcing fillers like silica are added to the PDMS chains. The resulting mixture is shaped and cured through a process known as vulcanisation. During this step, the uncured silicone rubber is exposed to heat and curing agents, such as peroxides or platinum-based catalysts. This process creates cross-links between the polymer chains, solidifying the material and giving it the high-temperature resistance and durability required for demanding applications.
The manufacturing process for high-temperature silicone differs from that of general-purpose silicone primarily in the formulation and curing stages. High-temperature silicone is engineered with specialised additives and catalysts to enhance its thermal stability and resistance to degradation at elevated temperatures. The curing process often involves higher temperatures and the use of advanced cross-linking agents to ensure that the material can withstand extreme conditions without compromising its physical properties. In contrast, general-purpose silicone is designed for applications with moderate temperature requirements and may use less robust curing methods and additives.
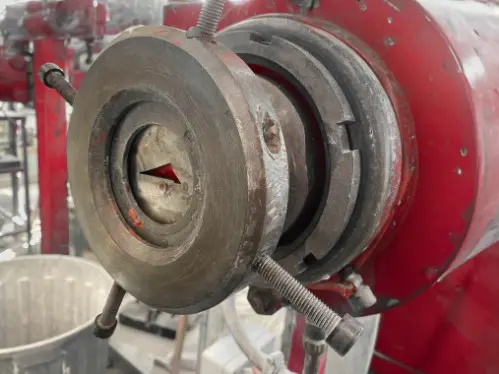
After curing, the silicone rubber undergoes rigorous testing to ensure it meets specific standards for heat resistance, mechanical strength and chemical stability. We can also customise the formulation with additional additives or adjustments to cater to specific industry requirements.
Advantages of High Temperature Silicone Rubber
High temperature silicone provides numerous benefits that make it suitable for challenging environments. Its thermal stability allows it to maintain flexibility and mechanical integrity over a wide temperature range, from freezing conditions to extremely high heat. This makes it an ideal choice for applications that require reliable performance in both extreme cold and hot settings.
Another significant advantage is its chemical resistance. It can withstand exposure to various oils, solvents and chemicals without degrading. This resilience ensures long-term durability in harsh industrial or environmental conditions. Additionally, its excellent electrical insulation properties make it particularly valuable for use in electrical and electronic applications where reliability is an important consideration.
Durability is another key feature of this material. In a similar way to general purpose silicone, high-temperature silicone rubber resists UV radiation, ozone and weathering. This makes it well-suited for outdoor applications. It remains effective over extended periods without significant performance loss. Moreover, specialised formulations can meet non-toxic and food-safe standards, making it suitable for use in food processing and medical industries.
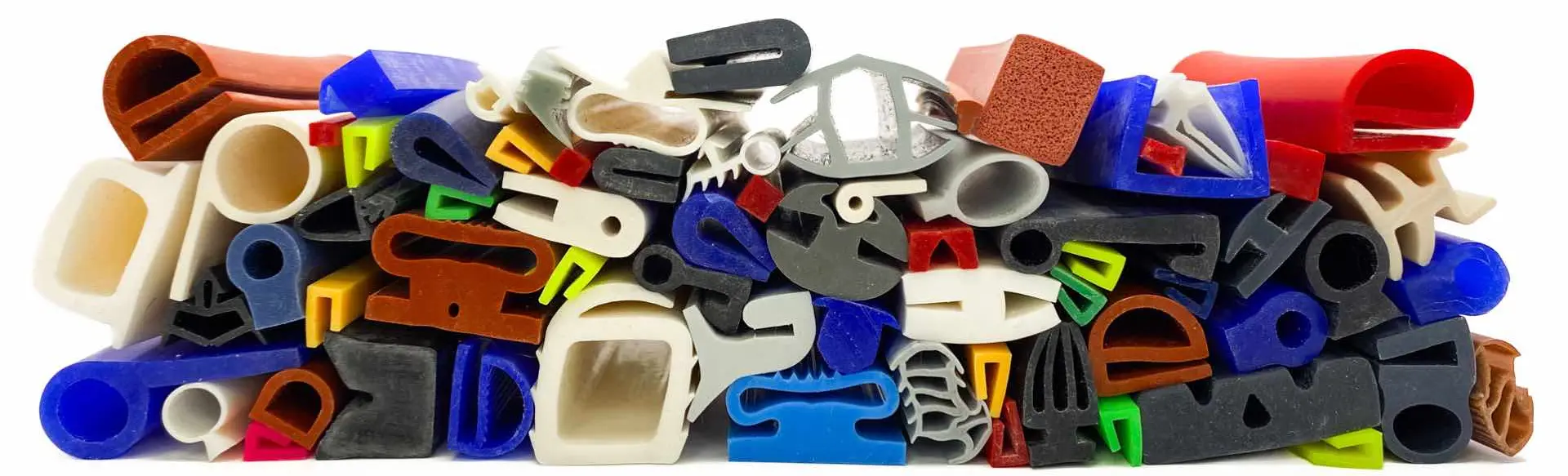
Flexibility and customisation further enhance the versatility of high-temperature silicone. It can be manufactured in various hardness levels, colours and forms, such as sheets, extruded profiles or moulded components. This adaptability ensures it can be tailored to meet the specific needs of different industries and applications.
Common Applications and Uses
High temperature silicone rubber’s versatility makes it indispensable across various industries. Its ability to perform reliably under extreme conditions has established its role as a superb material in numerous specialised applications.
Industries
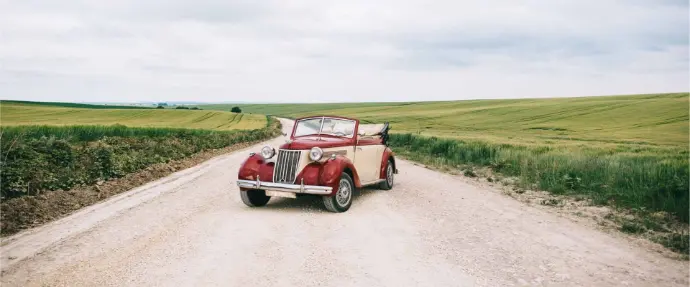
Automotive
In the automotive industry, high temperature silicone is commonly used for components exposed to high engine temperatures and harsh environments. These include gaskets, seals and hoses designed to handle the thermal stresses of internal combustion engines and hybrid systems. Additionally, its resilience to chemicals like engine oils and coolants ensures that silicone rubber parts maintain their integrity and performance over prolonged use. Automotive manufacturers also value its durability under exposure to UV radiation and ozone.
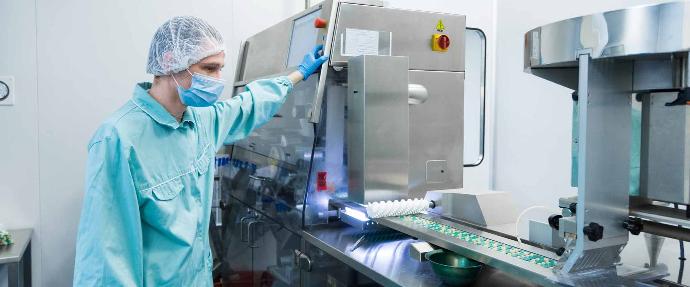
Medical, Pharmaceutical & Healthcare
The medical field also benefits significantly from high temperature silicone. It is widely employed in tubing, seals and medical devices that require repeated sterilisation at high temperatures. Silicones non-toxic and hypoallergenic properties make it safe for direct contact with human tissues, while its thermal stability ensures that it remains effective even after exposure to autoclaving processes. Furthermore, silicone rubbers flexibility and ability to be moulded into complex shapes allow for innovation in the design of medical tools and equipment.
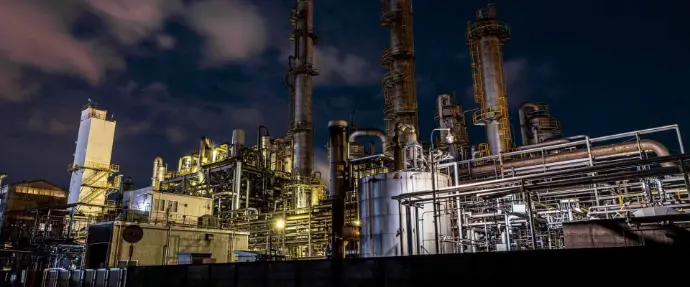
Industrial
In industrial settings, high temperature silicone helps maintain the reliability and efficiency of machinery. It is used for seals, gaskets and rollers in systems that operate under extreme heat or in chemically aggressive environments. Industrial processes such as food processing, chemical production, and metal fabrication often demand materials that can withstand thermal cycling without losing their properties. Silicone rubbers resistance to wear and tear, combined with its low maintenance requirements, makes it a cost-effective choice for these demanding applications.
Material Compound Datasheets
High temperature silicone can be extruded in a range of different hardnesses, each suitable for different applications. The properties and characteristics of these hardnesses may differ. Please see the downloadable PDF material compound datasheets for this information.
Looking for a different grade of Silicone?
In addition to high-temperature Silicone, we are also able to manufacture rubber sealing products in a selection of other Silicone compounds. This includes general purpose silicone, metal detectable silicone, high tear strength silicone and flame retardant silicone.
Contact Us
With over 50 years' experience in the rubber sealing industry, our team has extensive experience in finding sealing solutions for our customers. Contact our experts via phone or email for sealing advice or bespoke quotations.
Email:
sales@sealsplusdirect.co.uk
Telephone:
01425 617722