A Complete Guide to Viton Rubber
What is Viton Rubber?
Viton rubber, a high-performance fluoroelastomer, demonstrates exceptional performance when exposed to challenging environments, including extreme temperatures and harsh weather conditions. As a synthetic rubber recognised for its excellent chemical resistance, it is invaluable across multiple industry sectors. Its robust sealing properties make it suitable for aerospace, automotive and chemical processing applications. Withstanding high temperatures and exhibiting low gas permeability, Viton remains the material of choice for sealing components in critical equipment and systems that require a material known for its reliability and longevity.
Viton is available in a commercial grade, known as Viton FKM, and genuine Viton™, a brand name for fluorocarbon rubber polymers of The Chemours Company. These materials offer different performances, resistance to chemicals and flexibility at low temperatures. They can be supplied as Viton sheet or extruded profiles.
This article provides a detailed background to the history of Viton and how it can be used for manufacturing bespoke sealing solutions. It also details the benefits of using this material for sealing applications.
How is Viton Rubber Made?
The history of Viton rubber shows a journey of innovation and adaption to meet the evolving needs of industries that require high performance elastomers. The mid-20th century saw an increased demand for synthetic rubbers with enhanced chemical resistance. Whilst the materials available at the time offered some resistance to chemicals, oils and fuels, they did not meet the challenges associated with some harsh environments.
In the 1950s, a team of chemists at DuPont developed a material that is considered to be the origin of Viton. This material was known for its outstanding chemical resistance, high-temperature stability and durability. Over the years the formulation of Viton evolved to meet specific industry demands. Different grades of Viton were developed to cater to various applications, ranging from automotive and aerospace to chemical processing. In 2015, DuPont moved the Viton brand into a separate company called The Chemours Company which continues to invest in the research and development of Viton materials.
Today, the basic principles for manufacturing Viton rubber involve combining vinylidene and fluoride with curing agents, accelerators and processing acids. This process allows for the adjustment of properties that influence the hardness, flexibility and chemical resistance of the manufactured compound.
Viton
rubber is typically extruded to a desired shape using a machine called an
extruder. This machine uses pressure and temperature to push the compound
through a tool (known as a die). The extruded profile is then cured and hardened
using a vulcanising line, steam line, salt bath or autoclave cure. However,
Viton can also be rolled and squashed to a required thickness to create large
Viton sheets of rubber using a calender roller.
Advantages of Viton Rubber
Viton rubber boasts many advantages for manufacturing custom extrusions. As a compound with exceptional chemical resistance and resilience in harsh environments, it is often the material of choice for industries that require reliability. Some of the advantages that make Viton dependable for sealing applications include;
- Chemical
Resistance: One of the most sought after benefits of Viton is its
resistance to chemicals, oils, fuels and solvents. As a material that remains
stable when in contact with corrosive elements, Viton provides a reliable
choice for applications where other materials may fail. Viton is also
hydrophobic, which means that it repels water and resists the penetration of
oil and water-based liquids.
- Temperature
Range: Operating within a temperature range of -15°C to 205°C, Viton rubber
is known for its excellent temperature resistance. It maintains its mechanical
properties at elevated temperatures, making it suitable for applications where
it will be exposed to high heat. As well as withstanding temperatures up to 205°C,
Viton seals can also withstand short intermittent exposure of approximately 300°C.
Viton also remains flexible below freezing without cracking, splitting or any
other degradation of its physical properties. These characteristics make it
suitable for exceptionally low and high-temperature environments, such as
aerospace and industrial settings, where exposure to extreme temperatures is likely.
- Weathering: As Viton can withstand exposure to the elements, it is suitable for use in outdoor environments. It is relatively inert to ultraviolet (UV) so will not degrade or discolour when installed in areas subjected to prolonged sunlight exposure. Viton also demonstrates outstanding water resistance and is impermeable to moisture.
As well as exhibiting excellent resistance to most substances, fluids and environmental elements, Viton offers further characteristics that position it as a versatile and high-performance material. These characteristics include;
- Low Gas
Permeability: Although the permeability of gases is influenced by factors
such as temperature and pressure, Viton has low gas permeability. This is
beneficial in sealing applications as it limits the passing of corrosive or
reactive gases that may degrade the material or compromise its structural
integrity. Gas impermeability also provides a level of insulation helping
maintain temperature and pressure within a specific area.
- Durability:
Viton has a unique set of robust mechanical properties that ensures consistent
performance and provides durability in most sealing applications. Together with
this ability to withstand most fluids, Viton is suitable for tough and dirty environments
without the risk of degrading or deteriorating.
- Elasticity
and Flexibility: Unlike some other synthetic compounds, Viton demonstrates
good tensile strength. This makes it flexible, resilient and able to maintain its
shape and function under stress.
- Low
Compression Set: Products manufactured from Viton exhibit a good resistance
to compression set by retaining their original shape and sealing properties
after compression. Unlike other materials that are damaged with prolonged
compression, Viton ensures reliable performance.
- Resistance to Aging: Viton demonstrates resistance to aging and degradation which contributes to long-term reliability. Prolonged exposure to most fluids will not cause the rubber to degrade.
Disadvantages of Viton Rubber
While Viton rubber offers many advantages in tough and hostile environments, there are a number of potential disadvantages that may make it unsuitable for certain applications. In some cases, the disadvantages may be outweighed by the materials unique combination of properties, whilst in others, an alternative elastomer may be more appropriate. Some of these disadvantages include;
- Cost:
As a high-performance material, Viton is significantly more expensive than
other synthetic rubber compounds due to the manufacturing process and raw
material cost. However, the higher cost can often be justified when considering
that its resistance to aging and longevity allows you to purchase a product
that needs to be replaced less frequently than sealing solutions manufactured
from other materials.
- Hardness:
Depending on the specific formulation, Viton rubber can be relatively hard
compared to other materials. For applications that require a softer or more
flexible material you may choose to consider alternative materials, such as EPDM or
Silicone, which can be extruded in a selection of hardnesses.
- Limited Resistance to Certain Chemicals: Although Viton provides excellent resistance to most substances, it may experience a small degree of swelling if exposed to certain chemicals. These include Skydrol, amines, esters and hot hydrofluoric acids. It is essential to carefully evaluate any contact substances to determine if Viton is the most suitable material.
Common Applications and Uses
Viton is a well-established and trusted material that plays a critical role in sealing solutions for demanding environments across various industry sectors. These products can be manufactured to order from both Viton FKM and genuine Chemours Viton to suit the desired application and budget. Although it is best to select a material based on the environment it will be used in, Viton is an exceptional material with excellent all-round properties that makes it suitable for most applications. Viton sheet and seals are commonly supplied to the following industry sectors.
Industries
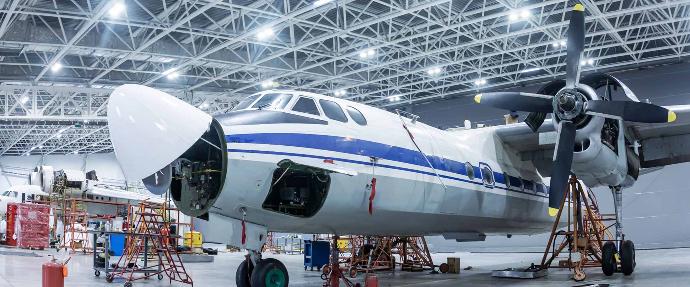
Aerospace
Viton fluoroelastomers have excellent fuel and heat resistance so are ideal for aviation and space exploration activities on aircraft, spacecraft and satellites. Demonstrating a higher resistance to aging and degradation than other non-fluorinated elastomers, Viton is often the material of choice for modern aircraft systems.
The characteristics of Viton create reliable sealing solutions that prevent the leakage of fluids whilst withstanding extreme temperatures and resisting exposure to harsh chemicals, such as aviation fuels and hydraulic fluids. It is commonly used for sealing applications in aircraft engines, fuel handling systems and other environments that require high temperature resistance and a low compression set.
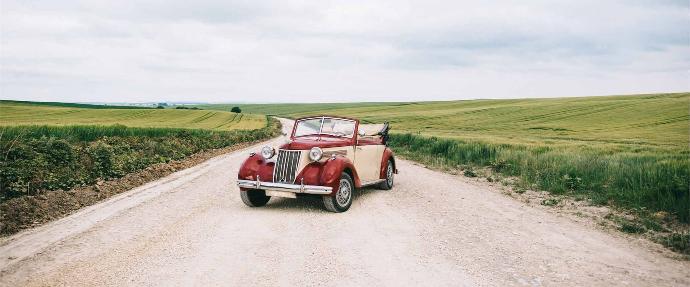
Automotive
Similarly to the aerospace industry, Viton is relied upon in automotive applications for its diverse range of high-performance characteristics. Whilst other materials are regularly used in the production of window and door gaskets, Viton rubbers exceptional chemical resistance and high-temperature stability make it the best material for sealing and protecting critical equipment and components. This includes fuel system components, engine gaskets and exhaust systems helping prevent leaks and ensure the integrity of the system.
Viton O-rings are also widely used in automotive applications where resistance to fuels, lubricants and high temperature is necessary. They are commonly used in fuel injectors and fuel pumps.
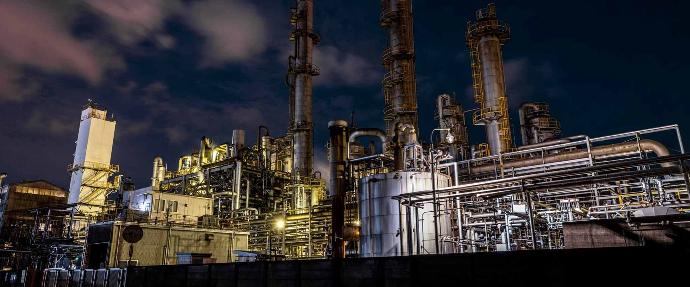
Chemical Processing
As a material that can withstand contact with almost any substance, Viton rubber is widely used in chemical processing due to its excellent resistance to chemicals, acids and solvents. It can be used to create a reliable barrier between different fluids and prevent leaks, even in the presence of aggressive chemicals. The chemical resistance, high-temperature stability and overall durability of Viton make it a preferred material in chemical processing applications where maintaining a seal and preventing chemical leaks are critical to safety and operational efficiency.
It is also possible to apply a Viton coating to equipment surfaces that come into direct contact with corrosive chemicals to provide an additional layer of protection.
Types and Grades of Viton Rubber
Whilst Viton is generally resistant to weathering, extreme temperatures and harsh chemicals, the specific performance may vary depending on the exact type of material used. Viton is available in two variants; genuine Viton™ and Viton FKM, which is a lower cost copy with similar characteristics. These variants can be manufactured in different grades containing different amounts of fluorine which has an impact on its resistance to chemicals. As the percentage of fluorine increases, its flexibility at low temperatures decreases.
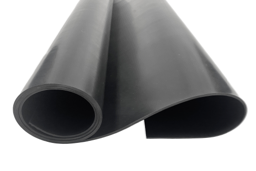
Genuine Chemours Viton
™
Genuine
Viton™ is manufactured by The Chemours Company and offers the best resistance
to most substances and high temperatures. While being more expensive than Viton
FTM, it is incredibly durable and resilient. It is available with a hardness of
70°sh A.
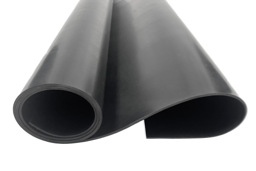
Viton FKM
Viton
FKM is a lower cost material that exhibits similar properties to Genuine
Chemours Viton™ and offers an affordable solution for most applications. Commercial
grade Viton is available with a hardness of 75°sh A.
Contact Us
With over 50 years' experience in the rubber sealing industry, our team has extensive experience in finding sealing solutions for our customers. Contact our experts via phone or email for sealing advice or bespoke quotations.
Email:
sales@sealsplusdirect.co.uk
Telephone:
01425 617722