A Complete Guide to Sponge Rubber
What is Sponge Rubber?
Sponge rubber, also known as expanded foam rubber, is a versatile and resilient material that finds widespread use across various industries. Made from synthetic rubber and silicone compounds, sponge rubber has an expanded cellular construction that is flexible and compressible. It is commonly manufactured with a closed-cell structure so does not absorb water and can be used to stop water ingress. Sponge seals manufactured from these materials demonstrate a level of durability that meets the demanding requirements of a diverse range of sealing applications. As well as being suitable for creating watertight seals, it can also be used for shock-absorbing and cushioning.
Due to its unique set of characteristics, sponge rubber can be extruded to create bespoke sealing solutions, cut into strips or manufactured into complex gaskets. These can be supplied with and without adhesive backing.
This guide explains the process for manufacturing sponge rubber seals, and discusses the advantages and disadvantages of using this material in sealing applications.
How is Sponge Rubber Manufactured?
The origin of sponge rubber dates back to the early 20th century where there was a growing demand for compressible materials that could be used to create reliable sealing solutions. Researchers discovered that adding a foaming agent to liquid latex and then mixing the material would produce a cellular structure with sponge-like properties. Over the years, these processes have been advanced through developments in chemical engineering and manufacturing. This progression has further refined the process used to manufacture sponge seals, enhancing their performance characteristics and expanding their range of applications.
Today, the process of manufacturing expanded sponge rubber products involves adding additives, such as curing agents and accelerators, to the raw rubber compound. The combined mixture is then mechanically whipped which helps evenly distribute the foaming agent throughout the compound. These foaming agents release gas when heated which generates bubbles in the material. This process creates a cellular structure within the rubber, resulting in a closed-cell spongy texture. The exact manufacturing steps may slightly vary depending on the specific type of rubber material and its intended application.
This sponge rubber compound can be used to create extruded profiles, gaskets or flat sheets. Extruded sponge seals are manufactured by pushing the chosen rubber compound through an extrusion tool (known as a die). This process is completed using an industrial extruder which uses pressure and temperature to extrude the required shape. The heat during this procedure causes the foaming agents to release gases and creates a closed-cell cellular structure within the rubber. Sponge seals manufactured using this method have a smooth glossy skin so can be used for applications where the product will be visible.
Sponge rubber can also be supplied in cut lengths. This process starts by pouring the chosen rubber compound into a large rectangular tank, usually 2 metres wide by 1 metre long. This creates a large block of rubber that can be horizontally sliced to the required thickness. These rectangular sheets are then vulcansed end-to-end to create a 6 metre long length which is carefully rolled into a ‘log’ and cut using a cutting machine to the required width.
It is possible to apply an adhesive backing to most sponge seals and strip during the manufacturing process.
Advantages of Sponge Rubber
Sponge seals can be manufactured from a large range of materials and offer a reliable general purpose solution for most sealing applications. Allowing for the creation of seals that aim to stop water ingress, sponge rubber offers a unique set of properties that cannot be found in solid rubber. Some of the advantages that make sponge rubber a dependable material include;
Compressibility
One of the key benefits of sponge rubber is its ability to compress and fill irregular gaps. When positioned between two surfaces, sponge sections are fairly soft so easily squash to create seals that stop the ingress of water, dirt and air. A sponge seal should return to its original shape and dimensions once the compression has been removed. However, excessive compression may cause permanent deformation of the seal. This is known as compression set which refers to the deformation or loss of thickness experienced by a material that has been subjected to excess force over an extended period of time. Compression set can be avoided by adjusting the compression force so that the sponge section is compressed by approximately a third.
The force required to compress seals manufactured from sponge rubber is determined by the construction of the section and type of material used. With low closing forces, it is often necessary to use a profile that has a hollow centre. This aids compression and makes the seal significantly easier to compress. Sponge rubber can also be manufactured in a selection of densities which influences its hardness.
Closed-Cell Structure
Sponge rubber can be manufactured with either an open or closed-cell structure. Whilst both materials present a similar appearance, they have very different properties that make them suitable for different applications. Open-cell sponge is softer, permeable to water and has less resistance to compression. This is useful for applications such as absorbing and reducing sound, but has obvious limitations for creating reliable watertight seals.
Closed-cell sponge has a structure that prevents the passage of air, water and other fluids which makes it resistant to the absorption of liquids and gasses. This is ideal for sealing solutions in both exterior and interior applications that are installed to act as a barrier to moisture, heat and sound. Closed-cell sponge rubber also has a tendency to recover to its original shape and size more effectively after compression.
Water and Weather Resistance
The majority of products manufactured from closed-cell sponge rubber materials are used as sealing solutions that aim to prevent water ingress. As closed-cell sponge is inherently resistant to the absorption of water and other fluids, it is suitable for outdoor sealing applications, as well as in environments where exposure to moisture is a concern.
The weather resistance properties of a particular sponge rubber section will be dependent on the material that it has been manufactured from. However, due to its relatively low price and desirable characteristics, most sponge seals are made from EPDM which is able to withstand exposure to weathering, ozone and UV.
Lightweight and Flexible
The density and weight of sponge rubber, whether in open-cell or closed-cell form, is lower than comparable materials, such as solid rubber, plastic and metal. The lightweight nature of sponge is advantageous in industries where weight is a critical factor. As most sponge seals are made from closed-cell materials, they are also buoyant and suitable for flotation devices or marine applications.
The flexibility of sponge rubber is a result of its cellular structure. Closed-cell sponge has a resilient feel that provides a degree of stiffness while retaining flexibility. This allows the material to conform to irregular surfaces.
Versatility in Formulations
The type and formulation of sponge rubber can be tailored to
meet specific requirements, allowing for a wide range of hardness, flexibility
and other properties. As each type of rubber has a unique set of characteristics,
it is possible to select a material that is suitable for the environment that
it will be used in, as well as any substances that it may come into contact
with. This includes applications requiring a sealing product that is resistant
to heat, chemicals or weathering.
It is also possible to add pigments to some silicone and rubber compounds to create sponge seals in various colours. This is desirable for applications that need to match company branding or provide an aesthetic appearance.
Common Applications and Uses
The individual advantages of each type of rubber further expand their use in different environments. The chemical and environmental resistance properties of each rubber compound should be considered when choosing a particular material to ensure a long-lasting and reliable sealing solution is installed. Although each material has a unique set of characteristics, sponge rubber is an all-round general purpose product that offers a reliable sealing solution for most applications. Sponge seals are commonly manufactured and used for the following applications;
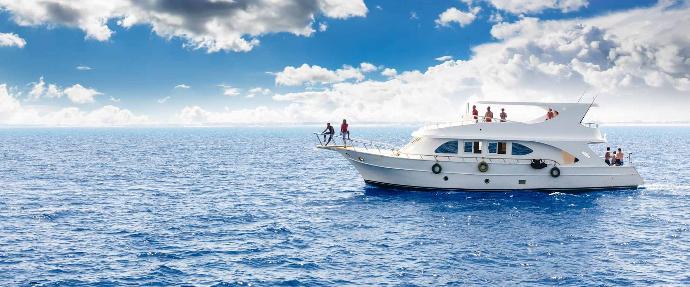
Sealing Solutions
Sponge seals are widely used in various industry sectors to create dependable sealing solutions that prevent water ingress. Typically manufactured from EPDM, sponge seals are highly resistant to weathering and UV rays, making them suitable for indoor and outdoor environments. By compressing a sponge rubber section by approximately 30%, you can create a reliable seal that does not suffer from the effects of compression set.
These seals are available in different forms, such as extruded sections, cut strips or custom gaskets in a variety of shapes and sizes.
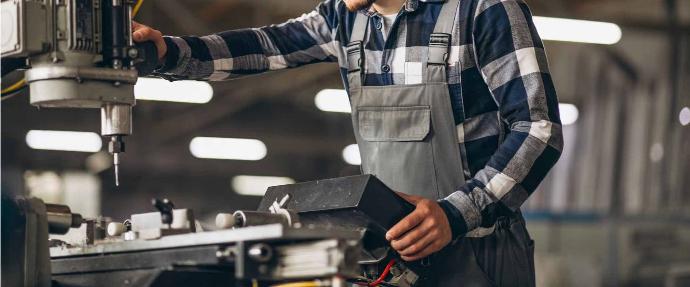
Cushioning and Padding
Sponge rubber is a material that has great cushioning and shock-absorbing properties. It's often used to protect windows and sensitive equipment. Sponge seals made of this compressible and resilient material can be inserted between two surfaces, reducing imperfections and creating a reliable watertight seal.
In addition to its sealing properties, sponge rubber is also useful in industrial applications as a vibration dampener. It can be placed between machinery and surfaces to absorb vibrations, impact, and reduce noise levels. Sponge rubber is available in various thicknesses and densities, making it a versatile material for different applications.
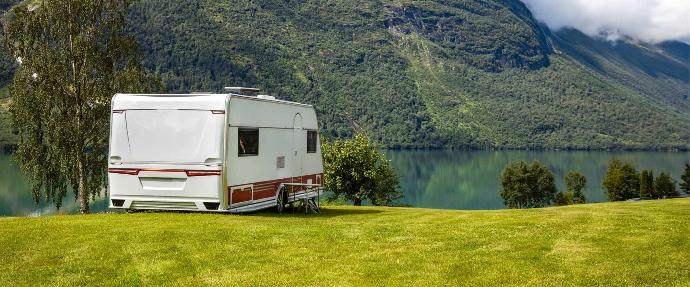
Insulation
Sponge rubber is a highly effective insulator that can trap air within its cellular structure. It offers protection against heat, sound, and vibration, making it a valuable component in HVAC systems. By preventing heat loss or gain during the transfer of air, it helps improve the overall energy efficiency of the system.
Sponge rubber is also great at absorbing sound, making it an ideal choice for acoustic insulation in buildings, vehicles, and industrial equipment. It helps dampen vibrations and reduces the transmission of noise, making it a versatile solution for noise control in a variety of settings.
Types of Sponge Rubber
Sponge rubber is a type of product that can be manufactured from various rubber and silicone compounds. The choice of sponge rubber depends on factors such as the intended use, environmental conditions and required performance. These materials have different characteristics and choosing the correct compound is essential for providing a long-lasting sealing solution that does not degrade or deteriorate. It is possible for these compounds to be blended to create hybrid rubber materials with enhanced properties or lower production costs. Some common types of sponge rubber include;

Neoprene Sponge Rubber
Neoprene
sponge is known for its excellent resistance to water, oil and chemicals. It
provides good weathering and ozone resistance, making it suitable for outdoor
applications. Neoprene is often used in seals, gaskets and weather strips.

EPDM Sponge Rubber
EPDM
(Ethylene Propylene Diene Monomer) sponge rubber is known for its outstanding
weather resistance, UV resistance, and ozone resistance. It is commonly used in
outdoor applications where exposure to the elements is a concern. EPDM is often
used in automotive seals, gaskets, and weather stripping.

Nitrile Sponge Rubber
Nitrile
sponge rubber, also known as NBR is oil-resistant and exhibits good mechanical
properties. It is commonly used in applications where resistance to oils,
fuels, and greases is crucial. Nitrile sponge rubber is often used in seals for
oil and gas equipment.

Silicone Sponge Rubber
Silicone
sponge rubber has a wide temperature range and excellent resistance to extreme
temperatures, making it suitable for high-temperature applications. It is often
used in aerospace, electronics, and medical applications.

Polyurethane Sponge Rubber
Polyurethane
sponge rubber is known for its high load-bearing capacity and durability. It is
often used in applications where a combination of cushioning and durability is
required, such as in furniture and automotive seating.
Contact Us
With over 50 years' experience in the rubber sealing industry, our team has extensive experience in finding sealing solutions for our customers. Contact our experts via phone or email for sealing advice or bespoke quotations.
Email:
sales@sealsplusdirect.co.uk
Telephone:
01425 617722