A Complete Guide to PVC Extrusions
What is a PVC Extrusion?
PVC, an abbreviation for polyvinyl chloride, is a common synthetic polymer and plastic used for manufacturing PVC extrusions and seals. It is known for its versatility, chemical resistance and low price. Second only to polyethylene, PVC accounts for over 20% of all plastics manufactured worldwide and has become a material used extensively across almost every industry sector. Its global success and mass production has helped develop a durable plastic compound at a relatively low cost that can be used for most sealing and decorative applications.
This guide provides a detailed background to the history of PVC and explains how it can be used for manufacturing bespoke PVC extrusions. It also details the main advantages and disadvantages of using this material for sealing products.
How Are PVC Extrusions Manufactured?
The first significant step in the development of PVC occurred in the 19th century when chemists began exploring vinyl chloride. This is a gas that was produced as a by-product in the production of other chemicals. Later that century, chemists developed a method for making a stable and flexible PVC material that involved using a combination of heat and chemical stabilisers. This produced a polymer that is considered to be the origin of modern PVC. The commercial potential of PVC was quickly recognised and initially used in insulated electrical wiring and coatings for fabrics. In today’s world PVC is a common household name and is used for making pipes, window frames, PVC extrusions and decorative trims.
PVC extrusions are manufactured from plastic granules that are heated, mixed and fed into a machine called an extruder. This machine uses pressure and temperature to push the melted compound through a die. This die, also known as a tool, contains a cut out that allows the machine to extrude the correct profile shape. It is often necessary to pull the extrusion through the die to apply consistent tension and avoid the section distorting or being manufactured with inconsistencies. Unlike rubber sections, PVC extrusions do not need curing and are hardened during the extrusion process. However, it is often essential to cool the section in chilled water after it has been extruded to stop it from deforming when coiled.
As an incredibly versatile material, PVC can be used to manufacture flexible or rigid sections in various hardnesses. In a similar way to synthetic rubbers, this plastic compound can be co-extruded allowing for the production of a duel density product that contains both soft and hard materials.
It is possible to apply various finishing options to PVC extrusions during and immediately after the extrusion process. This includes colour matching, cutting set lengths, printing and the application of adhesive tape.
- Colour
Matching: Unlike synthetic rubber, plastic sections can be extruded in
almost any colour using a RAL or Pantone colour reference. The material is coloured during the compounding process by incorporating pigments into the
mixture. PVC can also be extruded in translucent materials.
- Cutting
to Length: Although profiles are
normally extruded in long continuous lengths, PVC extrusions can be cut to
shorter lengths during the manufacturing process. This is achieved after the
section has been pulled through the die using an automated cutting machine that
measures and cuts the section to the required pre-determined length.
- Printing:
Extruded plastics can be labeled using specialist inkjet printers that print
directly onto the section. This is a complicated process as the surface needs
to be properly prepared to ensure sufficient ink adhesion.
- Adhesive Tape : It is also possible to apply an adhesive backing to the seal whilst it is being extruded. Although this can be achieved at the time of installation, it is often preferable for the adhesive backing to be applied during the manufacturing process to simplify the installation.
Advantages of PVC
PVC is a versatile and lightweight plastic that offers several advantages compared to rubber compounds. As well as being a low-cost mass produced material, PVC extrusions demonstrate an excellent resistance to weathering and most chemicals. Some of the key advantages that make PVC a reliable material for sealing and decorative applications include;
- Weathering:
Used extensively within the glazing and roofing industries, PVC has excellent resistance to water and the effects of weathering. It exhibits
remarkable durability and stability when exposed to various environmental
elements such as UV, ozone, water or oxygen. PVC is also inherently resistant
to moisture and does not absorb water. Extrusions and trims can be used with
confidence in outdoor environments without the risk of degradation,
discoloration, swelling or warping.
- Chemical Resistance: PVC is resistant to a wide range of chemicals, including acids, cleaning fluids and some solvents. This allows extrusions and trims manufactured from this material to be used within environments where exposure or contact to these substances is likely.
As well as demonstrating an excellent resistance to most substances, products made from PVC also display exceptional functional characteristics that further expand their application. These characteristics include;
-
Cost-Effective
:
As a material used within almost every industry sector, the mass production of
PVC allows extrusions manufactured from this plastic to be produced at a lower
cost than those made from comparable rubber compounds. They also need to be infrequently
replaced due to the materials durability and longevity. The initial low production
cost coupled with the materials long lifespan makes PVC an affordable solution
for most applications.
- Lightweight:
PVC is also a lightweight plastic that can be used in situations where
weight is a concern.
- Versatility:
As a highly versatile material, PVC can be formulated to meet specific
requirements and demands. Polyvinyl chloride can be extruded in rigid or flexible
lengths, including co-extrusions containing multiple hardnesses. It can also be
extruded in almost any shape of any size.
- Hygienic
Properties: The hygienic properties of PVC allow seals manufactured from
this material to be used within the medical and pharmaceutical industry. As a
plastic resistant to bacteria and fungi, PVC can be used on medical devices and
equipment. Its chemical resistance also allows it to be cleaned with harsh
chemicals and cleaning fluids without the risk of degrading.
-
Fire
Resistant
: PVC is inherently flame resistant and has a low risk of
combustion. It has a high ignition temperature and can be used with confidence
in environments where fire resistance is important.
Disadvantages of PVC
While PVC offers many advantages in the production of custom extrusions and trims, there are occasions where alternative materials, such as synthetic rubber compounds, may be better suited to the required application. Some of the disadvantages of PVC that should be considered include;
- Environmental
Concerns: As the reliance on PVC grew, concerns were raised regarding its
environmental impact and the release of chlorine gas during production. However,
efforts have been made to develop more environmentally friendly formulations
with further regulation on its production and use. It is also possible to find
recycling programs for old products manufactured that are no longer required.
- Temperature Range: PVC has an operating temperature range between -5°C and 60°C which may make it unsuitable for some environments and applications. PVC can become stiff and brittle at low temperatures which may affect its resistance in cold climates. It can also become soft, lose its rigidity and start to decompose in temperatures that exceed 60°C.
Common Applications and Uses
PVC
extrusions, known for their durable construction and resistance to most
substances, are suitable for a wide range of applications across most industry
sectors. These seals and decorative trims can be manufactured to order in a
large selection of colours and hardnesses. Although it is best to select a
polymer based on the environment it will be used in, PVC is a material that has
excellent all-round characteristics. PVC sections are commonly supplied to the
following industries.
Industries
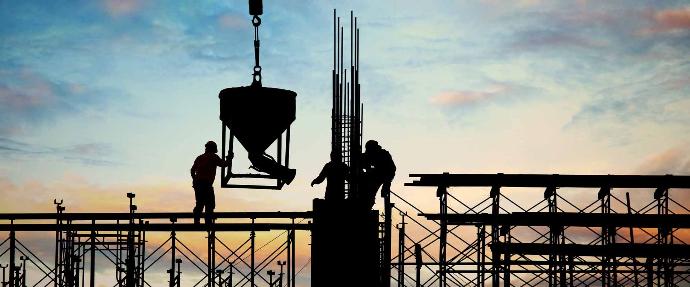
Construction
PVC extrusions are widely used in the construction industry for window and door frames, as well as seals, trims and mouldings. Seals used within this environment often need to be manufactured from lightweight, durable and low-maintenance materials that are resistant to the effects of weathering. As a material that can withstand sunlight, rain and most temperatures, extrusions manufactured from this material do not degrade or become brittle when exposed to these elements.
The Building Research Establishment (BRE) evaluates building materials based on their environmental impact, safety and performance. They have stated that PVC contains favourable properties and is one of the best all-round and long lasting materials for the construction industry.
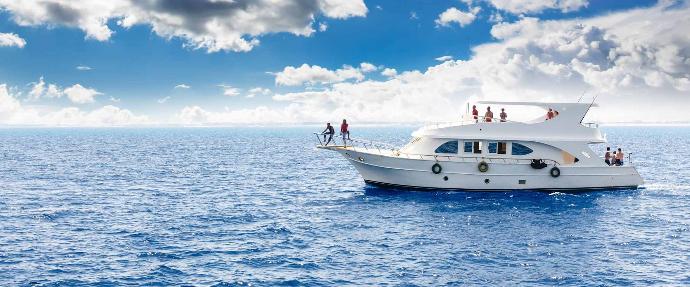
Marine
A large number of sections used within the marine industry are manufactured from PVC. Seals, tubing and decorative trims are commonly made from this material due to its low cost and excellent resistance to most environmental elements. These applications demonstrate how PVC is suitable for harsh and hostile applications without degrading or discolouring. PVC is also naturally resistant to moisture and does not absorb water.
Due to its non-marking properties, PVC is often the preferred material for manufacturing boat fenders. Unlike products manufactured from EPDM, PVC will not leach colour onto your boat or other surfaces in the event of impact.
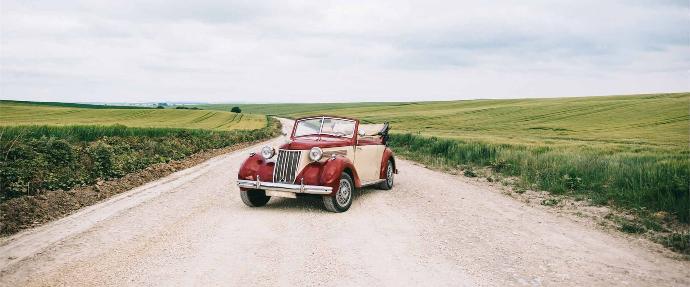
Automotive and Caravanning
PVC has favourable properties for use within the automotive and caravanning industry. Although most sealing products, such as window and door seals, are manufactured from EPDM, PVC is often used within this sector for decorative and insulating products such as trims and cover strips. As a material that can be extruded in any colour, it allows for a neat solution in instances where the product will be visible. It is also highly flexible whilst retaining its structural integrity.
As PVC has good resistance to oils and fuels, it can be used with confidence in automotive environments where there is possible contact with these substances.
Types and Grades of PVC
PVC is available in a diverse range of forms and hardnesses for different applications and industries. Although the initial compound is always the same, polyvinyl chloride can be extruded into rigid and flexible products by adjusting the formulation and amount of plasticisers. During manufacture, PVC can also be blended with synthetic rubber compounds, such as Nitrile, to create products with increased resistance characteristics at a lower cost.
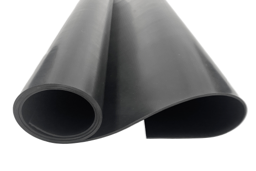
Rigid PVC
This
type of PVC is hard and inflexible. It is commonly used in the construction
industry for manufacturing pipes, fittings and other products where rigidity is
essential. Extrusions manufactured in this material are limited in length to
around 3 metres due to their rigid structure and inability to be coiled.
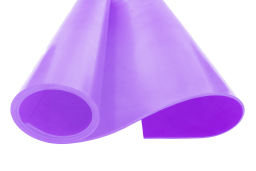
Flexible PVC
Flexible
PVC is softer and more flexible than rigid PVC. It contains plasticisers that
enhance its flexibility. Flexible PVC is often used for products such as
electrical cable insulation, medical tubing and decorative trims. Extrusions
manufactured in flexible PVC can be extruded in incredibly long lengths between
50 to 250 metres, depending on the size of the section.
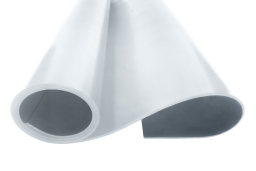
Food Grade PVC
Food grade polyvinyl chloride is a type of PVC
that is specifically formulated and manufactured to meet the safety and
regulatory standards for contact with food and potable water. It is essential
for materials used in the food industry to be safe and not transfer harmful
substances to the food or beverage being transported or stored.
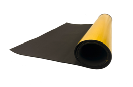
Expanded Nitrile / PVC Closed-Cell Sponge Rubber
PVC can be blended with Nitrile to create compressible closed-cell watertight seals to stop water ingress. The combination of these two materials helps reduce production costs whilst still offering some resistance to oil and fuel. This material can also be used as a thermal insulator.
Contact Us
With over 50 years' experience in the rubber sealing industry, our team has extensive experience in finding sealing solutions for our customers. Contact our experts via phone or email for sealing advice or bespoke quotations.
Email:
sales@sealsplusdirect.co.uk
Telephone:
01425 617722