A Complete Guide to Solid Rubber
What is Solid Rubber?
Solid rubber is a versatile and resilient material that is known for its resistance to wear and tear. Made from natural rubber, synthetic rubber or silicone compounds, solid rubber finds widespread use across a diverse range of industries. It has a solid construction that has similar characteristics to sponge rubber but without any air pockets within its structure. Available in different forms in a selection of materials, solid rubber demonstrates a level of durability that meets the demanding requirements of most sealing applications. As well as being used in the production of extruded sections for creating watertight seals, solid rubber can also be used for shock absorbing, cushioning and insulation.
Thanks to their unique set of properties, solid rubber materials can be extruded to create bespoke sealing solutions, cut into strips, or cut from large sheets to make complex gaskets.
This guide discusses the process required to manufacture sealing solutions in solid rubber materials. It also details the main advantages of each of these materials.
How is Solid Rubber Manufactured?
The history of solid rubber is intertwined with the developments of rubber itself, which has continuously evolved with advances in chemical engineering and manufacturing to be a staple material used within most industry sectors. One of the key developments in the history of solid rubber was the identification that the strength, elasticity and temperature resistance of rubber can be improved by heating the rubber compound during production. This vulcanisation process helped increase the popularity of solid rubber, allowing rubber compounds to be turned into different shapes and used for a variety of sealing applications.
Today, the process of manufacturing an extruded solid rubber sealing solution follows a very similar procedure. Whilst the specific details of the manufacturing process can vary based on factors such as the type of rubber, the complexity of the seal and its intended application, the generalised process involves material selection, preparation, extrusion, curing and finishing.
- Material Selection: A rubber compound should be chosen based
on the specific requirements of the application, such as temperature
resistance, durability and resistance to chemicals. Choosing a suitable
material is essential for providing a long-lasting sealing solution that will
not degrade or deteriorate. Common synthetic compounds used for solid rubber
seals include EPDM, Neoprene, Nitrile, Silicone, PVC and Viton.
- Material Preparation: Once a suitable material has been
identified, the rubber compound must be mixed with vulcanising agents,
accelerators and fillers to achieve the desired properties. The mixed compound
is then processed into a form suitable for the chosen manufacturing method,
either as sheets for cutting or extruded profiles.
- Extrusion: The mixed compound can then be used to create
extruded solid rubber profiles. This process uses pressure and temperature to
push the compound through a tool (known as a die) to extrude the required
shape.
- Curing: Once the rubber has been extruded it is subjected to a curing process, often referred to as vulcanisation. This involves exposing the rubber to heat, and sometimes pressure, to activate the vulcanising agents and create cross-links in the polymer chains. The curing time and temperature will depend on the rubber compound and the desired properties of the final seal. This can be completed on a vulcanising line, steam line, salt bath or autoclave cure.
Solid rubber can also be manufactured into flat sheets of
rubber that can be cut into narrow strips or used to create complex gaskets.
Once the chosen material has been identified and prepared, the raw rubber
compound is fed into a machine that uses a series of calender rollers to squash
the material. The spacing between the rollers can be adjusted to control the
thickness of the final rubber sheet.
Advantages of Solid Rubber
Seals, extrusions and other sealing products can be manufactured from a large range of solid rubber materials that provide a reliable solution for most applications. The overall choice to use solid rubber for manufacturing rubber seals is driven by its combination of durability, customisation options and cost-effectiveness. As a harder rubber, solid materials offer a greater resistance to abrasion, wear and other stresses that cannot be found with sponge rubber solutions. Some of the advantages that make solid rubber a dependable material include;
Water and Weather Resistance
Solid rubber is commonly used for manufacturing products that serve as sealing solutions to prevent water ingress. As a material that is inherently resistant to the absorption of water, solid rubber can be used in outdoor sealing environments where exposure to moisture and other fluids is a concern.
The weather resistance of a specific solid rubber profile is determined by the material that it has been manufactured from. Whilst most compounds have some resistance to the effects of weathering, most solid rubber sections are made from EPDM owing to its cost-effectiveness and favourable qualities. This material is able to withstand prolonged exposure to weathering, ozone and UV rays.
Versatility in Formulations
The composition and structure of solid rubber can be customised to meet specific requirements, allowing for a wide range of hardnesses, flexibilities and other properties. As each type of rubber has a unique set of characteristics, it is possible to select a material that is suitable for the environment where it will be used. This includes applications that require a solid rubber sealing solution that is resistant to chemicals, weathering or extreme temperatures.
Despite the name, solid rubber can also be manufactured in a range of hardnesses to suit the required application. This hardness is expressed between 40° Shore A and 90° Shore A, where 40° is comparable to a pencil eraser and 90° is similar to the hardness of a bath plug.
Additionally, certain silicone, rubber and PVC compounds allow for the addition of pigments, facilitating the creation of seals in different colours. This is advantageous for applications that need to be aligned with corporate branding, or sealing solutions that require a visually appealing appearance.
Durability
Solid rubber is known for its robustness and durability. The inherent resilience of these materials enables seals manufactured from solid rubber compounds to withstand prolonged use, resist wear and tear, and maintain their structural integrity over time. This durability is particularly important in environments where seals are exposed to challenging conditions, such as extreme temperatures, UV radiation and chemical substances. The ability to maintain effective sealing under these circumstances helps contribute to the seals longevity and ensures consistent performance.
As
a result of this durability, the robust nature of solid rubber provides an
extended service life, reduced maintenance costs and enhanced reliability. This
not only protects against environmental elements but also promotes efficiency
in sealing functions, providing a dependable sealing solution.
Chemical, Fuel and Oil Resistance
Whilst it is always best to choose a material resistant to the specific substances that it will come into contact with, the ability to manufacture rubber seals from a diverse range of compounds allows for the selection of a material most suitable to the target environment. The formulation of solid rubber, dependent on the specific material, equips these seals with the ability to withstand contact with various chemicals, solvents, fuels and oils. This resistance is particularly advantageous in industrial settings and manufacturing environments where seals are exposed to potentially corrosive substances.
Different materials are resistant to different substances and
choosing the correct material is essential to prevent the degradation, swelling
or breakdown of the rubber section.
Common Applications and Uses
With a diverse range of materials available, the individual advantages of each type of rubber further expand their use within different environments and industry sectors. Although solid rubber has a unique set of properties, it is an all-round general purpose product that offers a reliable sealing and edging solution for most applications. Solid rubber extrusions are chosen for their ability to maintain flexibility, resist wear and tear and effectively seal against environmental factors. They are commonly manufactured for the following purposes;
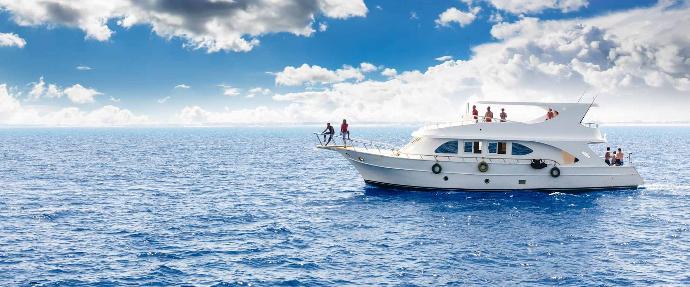
Sealing Solutions
Solid rubber has become a versatile material for producing sealing solutions that create a barrier between two surfaces to prevent the ingress of water, air or dust. Commonly manufactured from materials such as EPDM, most rubber seals exhibit excellent resistance to the effects of weathering making them highly suitable for indoor and outdoor environments. They are used in doors, windows and other locations where a secure and effective sealing barrier is required.
These profiles are available in a selection of materials in several different forms. This includes extruded sections, cut strips or custom gaskets.
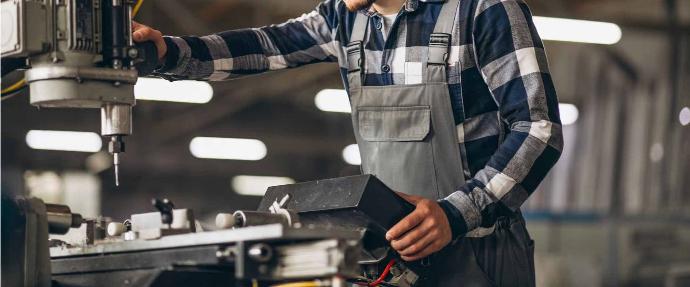
Cushioning Padding
Solid rubber materials are often used for cushioning applications due to their inherent resilience and shock-absorption capabilities. Their ability to deform and absorb energy demonstrates a versatile product that can be used to manufacture anti-vibration mounts and shock absorbers. Solid rubber can be placed between machinery and surfaces to absorb vibrations, impact and reduce noise levels. It can be extruded or cut into various sizes, making it an adaptable material for most protective applications.
These materials can also be extruded into sections and used as bumpers in automotive, marine and industrial applications to absorb shocks and impact. This helps protect surfaces and reduces the risk of damage.
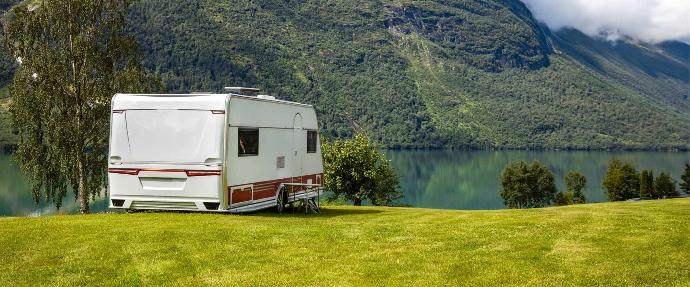
Edge Protection
Extrusions and trims, made from solid rubber materials, can be pushed over an edge to apply a neat and protective solution to various surfaces. Often referred to as safety edging, they help prevent damage to the underlying surface from impact, abrasion or environmental factors. Whilst commonly manufactured from compounds such as EPDM and PVC, edge trims are produced with a self-gripping metal spine that will hold itself in place without the need for additional adhesive.
Edge trims are commonly used within most industry sectors on doors, windows, hatches or any other surface that needs a protective edging solution.
Types of Solid Rubber
Solid rubber products can be manufactured from various rubber and silicone compounds. The material choice depends on factors such as the intended use, environmental conditions and required performance. These compounds have different characteristics and choosing the correct compound is essential for providing a long lasting sealing solution that does not degrade or deteriorate. It is possible for these compounds to be blended to create hybrid rubber materials with enhanced properties or lower production costs. Some common types of solid rubber include;
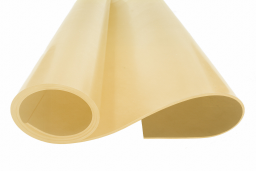
Natural Rubber
Derived from the latex sap of rubber trees, natural rubber is known for its high elasticity and resilience. It's used in various applications, including tyres, conveyor belts, and vibration mounts.
Styrene Butadiene Rubber
SBR is a synthetic rubber that offers good abrasion resistance and durability. It
is commonly used in the production of tyres, conveyor belts, and footwear.
Neoprene Solid Rubber
Neoprene
is a synthetic rubber known for its excellent resistance to oil, ozone, and
weathering. It is often used in gaskets, hoses, and weather-resistant
applications.
EPDM Solid Rubber
EPDM
rubber is known for its outstanding weather resistance, UV resistance, and good
chemical resistance. It is commonly used in outdoor applications such as seals,
gaskets, and roofing materials.
Nitrile Solid Rubber
Nitrile
rubber is appreciated for its excellent oil and fuel resistance. It is commonly
used in seals, gaskets, and hoses in automotive and industrial applications.
Silicone Solid Rubber
Silicone
rubber is known for its high-temperature resistance, flexibility, and excellent
electrical insulation properties. It is used in a wide range of applications,
including medical devices, cooking utensils, and automotive components.
Contact Us
With over 50 years' experience in the rubber sealing industry, our team has extensive experience in finding sealing solutions for our customers. Contact our experts via phone or email for sealing advice or bespoke quotations.
Email:
sales@sealsplusdirect.co.uk
Telephone:
01425 617722