A Complete Guide to Natural Rubber
What is Natural Rubber?
Natural rubber (NR) is made by extracting latex from trees and some plants. It is the raw material used to manufacture more than 45,000 products, such as elastic bands, surgical gloves and some rubber seals. Due to its excellent compression recovery, high elasticity and tensile strength, natural rubber has proven to be an excellent compound for manufacturing rubber seals that will be subjected to extreme pressures.
Although it is possible to manufacture synthetic alternatives to natural rubber with some of the same properties, it is not feasible to create a material with identical characteristics. The closest synthetic substitute to natural rubber is SBR but this does not match the natural resilience of NR.
This guide provides a background to the history and production of natural rubber and details the main advantages and disadvantages of using it for custom rubber products and gaskets.
How is Natural Rubber Made?
The origin of natural rubber dates back to 1600 BC when South American settlers used latex for medicines, clothing and footwear. By making a special incision into the trunk of a hevea brasiliensis tree, the trees bleed latex which could be collected for processing. Dipping cloth and other products into this liquid made these items waterproof and superior to wear and tear. Whilst revolutionary at the time, these products became sticky in the summer and cracked in the winter. This problem wasn’t solved until 200 years later where chemists invented the vulcanisation process which hardened rubber to prevent it from melting in warm weather and cracking in the cold.
Whilst the Brazilian Amazon was the only source of natural rubber in the early 1900s, over 90% of the supply to Europe is now imported from South East Asia. The technique used to harvest natural rubber from the hevea brasiliensis tree requires a process called ‘tapping’. This involves making a series of shallow cuts in the trees bark to make the tree bleed. This liquid, known as latex sap, can be collected in small containers. The collected latex is then mixed with a formic acid to promote coagulation which causes the latex to thicken and turn into a solid. After coagulation, the rubber compound can be extruded or rolled into sheets or strips for the production of various rubber products.
The process for extruding seals in natural rubber is similar to the process for extruding profiles in synthetic rubber compounds. The natural rubber coagulum is pushed through an extrusion tool (known as a die) on an extrusion machine. This machine uses pressure and temperature to extrude the material to the required shape. The extruded section is then vulcanised using a vulcanising line, steam line, salt bath or autoclave cure. This cures and hardens the rubber profile so that it does not melt or break down in extreme temperatures.
Natural rubber seals are frequently used for brass and bronze portholes, as well as making flat gaskets for applications that may be subjected to high compression forces. These products are cut to the desired width or shape from flat sheets which are created using a calender roller. This process involves rolling and squashing the raw natural rubber compound through a series of rollers until it reaches the required thickness.
Although most sealing applications that use natural rubber require a solid material, this compound can also be manufactured into expanded sponge rubber products. During the extrusion process, carbon dioxide, nitrogen or other nucleating agents are added to the compound to create a sponge-like cellular structure. The gas injection rate can be adjusted to achieve different densities depending on the firmness required.
Advantages of Natural Rubber
Natural rubber is a valuable material for a number of sealing applications. Whilst it does not have the same characteristics as synthetic rubbers, it is often the preferred material for projects that require a high elasticity product with superior tear and abrasion resistance. Some of the key properties of natural rubber include;
- High
Elasticity and Flexibility: Unlike rubber seals manufactured from synthetic
compounds, such as EPDM and Silicone, natural rubber demonstrates exceptional tensile
strength. This property allows it to stretch or compress and return to its
original shape without permanent deformation when the stress is removed. It is
also highly flexible so can be bent or twisted without cracking or breaking. These
characteristics are best demonstrated in the production of elastic bands which
use natural rubber as part of their formulation.
- Tear
Resistance: One of the most notable mechanical properties of natural rubber
is its high tear resistance which allows it to resist the propagation of a tear
or crack when subjected to extreme forces. This resistance is dependent on the
thickness of the material as thicker products will naturally have a higher
resistance to tearing.
- Abrasion and
Wear Resistance: Natural rubber can withstand abrasion and wear which makes
it suitable for applications where the seal will come into contact with
abrasive surfaces.
- Renewable
and Sustainable: As natural rubber is sourced from rubber trees, it is a
renewable resource harvested using responsible and environmentally friendly
practices. Although it takes six years for the hevea-brasiliensis tree to bleed
sap, they are perennial and will produce latex for between 25-30 years without
the need for replanting. The production of natural rubber is also governed by
certification schemes such as FSC and SNR-I which aim to verify and
promote sustainable rubber production practices.
A single hevea-brasiliensis rubber tree produces between 60kg and 150kg of rubber during its lifetime. This is enough rubber to produce 500,000 elastic bands!
Disadvantages of Natural Rubber
Although natural rubber is suitable for a select number of sealing applications, there are occasions where synthetic rubber compounds, such as EPDM, Nitrile or Silicone, would be better suited. Some of the key disadvantages of using natural rubber for manufacturing rubber seals include;
- Sensitivity
to Temperature: Although seals are vuluncaised during the production
process, these products can become soft and lose their elasticity at high
temperatures. They can also become
brittle at low temperatures limiting their use in extreme temperature environments.
The recommended temperature range for natural rubber is -20°C to 70°C.
- Susceptibility
to UV and Ozone: Natural rubber is also vulnerable to damage from
ultraviolet radiation and ozone exposure. Prolonged exposure to sunlight will
cause seals manufactured from natural rubber to degrade, crack and discolour.
There will also be a reduction in its mechanical properties that will affect other
characteristics such as its elasticity and flexibility. It is recommended that natural
rubber seals are used in enclosed environments such as portholes where they
will not experience constant UV exposure. Although it is possible to add UV
stabilisers to the rubber compound during manufacturing, it is often better to
select an alternative synthetic rubber with better UV stability for
applications that will encounter prolonged exposure to sunlight.
- Price Volatility: The production of natural rubber is a labour intensive process that can only be carried out on rubber plantations in regions with suitable climates. This can reduce availability and cause fluctuations in cost due to factors such as weather conditions and disease outbreaks that affect the rubber trees.
Common Applications and Uses
Natural rubber is a durable rubber compound known for its tensile strength, tear resistance and abrasion resistance. This makes it suitable for rubber seals used within a select number of industry sectors. These products can be manufactured to order from both solid natural rubber and expanded natural rubber to suit the desired application. Although it is best to select a rubber compound suitable for the exact intended use, NR can be used with confidence in enclosed environments that require good compression recovery. Natural rubber sealing solutions are commonly supplied to the following industries;
Industries
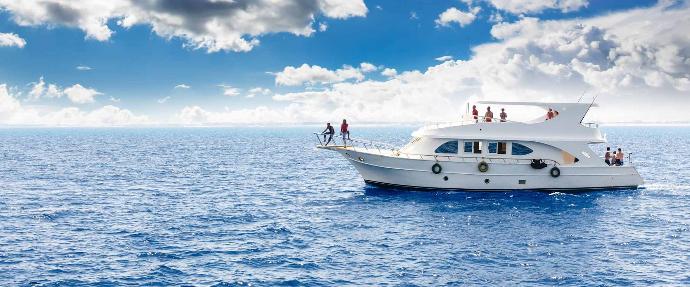
Marine
Natural rubber seals, such as porthole rubber strips, are used for sealing brass and bronze port lights and vents on boats and other marine vessels. As portholes are normally hinged and screw-clamped, they exert a large amount of force when closed. This makes it essential to use a rubber product, like natural rubber, with good compression recovery.
Watertight door and hatch seals are also manufactured using a natural rubber and SBR blend. These seals are used in heavy duty watertight doors, hatches and skylights with multiple latching points. In the same way as port lights, they subject the rubber seal to extreme compression so need to use a material with good recovery.
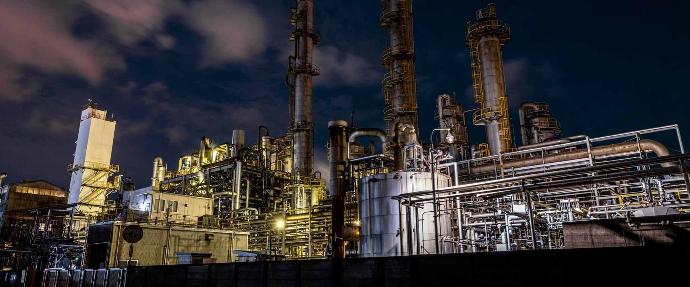
Industrial
Natural rubber is often used for industrial applications on equipment and machinery. Unlike most seals that are used to prevent water ingress, natural rubber products within this industry are often used in shot blast cabinets, conveyor belts and shoots on silos. The excellent tear and abrasion resistance of natural rubber makes this material suitable for these applications which will come into contact with abrasive surfaces and other substrates.
As
natural rubber has a poor resistance to chemicals, oils and solvents, it is
sometimes necessary to use alternative materials with similar abrasive
properties, such as Nitrile.
Types and Grades of Natural Rubber
Natural rubber is available in a selection of grades designed to suit different applications, uses and budgets.
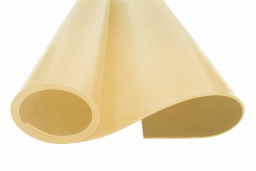
Commercial Grade Natural Rubber
As
natural rubber is fairly expensive it is often blended with other rubber
compounds to produce a cheaper quality material. Styrene-butadiene (SBR) is
commonly used with NR for instances where the material will not be subjected to
extreme duress, such as dust seals and protective pads. It is available in
economy and premium grades with a hardness of 70°sh A.
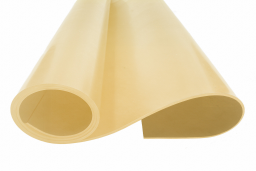
Natural Rubber to British Standard BS1154
Natural
rubber is also available in a grade compliant with British Standard BS1154
specifications. This material uses a higher content of natural rubber for high-performance applications that require maximum compression recovery and abrasion resistance.
It is available in a selection of hardnesses including Y40, Y50, Y60, Y70, Z40,
Z50, Z60 and Z70 where Y indicates white and Z specifies black.
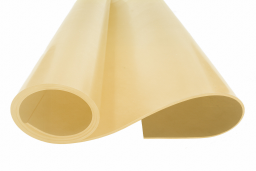
Tan Shotblast Rubber
Shotblast rubber has a higher abrasion
resistance than other grades of natural rubber. It is ideal for shot blast
cabinets and abrasive resistant applications. It is available with a hardness
of 45°sh
A.
Contact Us
With over 50 years' experience in the rubber sealing industry, our team has extensive experience in finding sealing solutions for our customers. Contact our experts via phone or email for sealing advice or bespoke quotations.
Email:
sales@sealsplusdirect.co.uk
Telephone:
01425 617722