Rubber seals are important to many applications, ranging from automotive engines and industrial machinery to household plumbing and medical devices. These sections are designed to prevent the leakage of fluids, gases or other materials by creating a reliable barrier between two surfaces. One of the key properties that determine the effectiveness of a rubber seal is its ability to maintain its original shape and dimensions under continuous pressure. This characteristic is known as compression set. As compression set directly impacts the seals performance and longevity, understanding this term is important for anyone involved in the design, selection or maintenance of rubber sealing products.
What is Compression Set?
Compression set is a measure of the permanent deformation that a rubber material undergoes after being compressed and then released. When a rubber seal is compressed, it deforms to fill the gap between the surfaces it is sealing. Ideally, when the compressive force is removed, the rubber should return to its original shape. However, in practice, rubber materials often experience some degree of permanent deformation, meaning they do not fully return to their original dimensions. This residual deformation is what is referred to as compression set.
Compression set is typically expressed as a percentage, representing the difference between the original thickness of the rubber and its thickness after the compressive force has been removed and the material has had time to recover. A lower compression set percentage indicates that the rubber has maintained more of its original shape, which is generally desirable for maintaining a reliable watertight seal. Conversely, a higher compression set percentage suggests that the rubber has deformed more significantly and may be less effective at sealing after prolonged use.
Causes of Compression Set in Rubber Seals
Several factors contribute to the compression set in rubber seals. This can influence how well they maintain their shape and function over time. These factors include the type of rubber material, the level and duration of compression, the operating temperature and the environmental conditions to which the seal is exposed.
Material Properties
The type of rubber material used in a seal is a primary determinant of its compression set characteristics. Different rubber compounds have varying levels of elasticity, resilience and resistance to deformation. For example, natural rubber is known for its high elasticity, which generally results in a lower compression set and makes it an excellent choice for applications where flexibility and quick recovery are important. However, natural rubber may not perform well in certain environments, such as those involving exposure to oils, chemicals or extreme temperatures, where synthetic rubbers might be more appropriate.
Synthetic rubbers, such as nitrile, silicone and EPDM, are often selected for their specific resistance to harsh conditions, including oil, heat and weathering. These materials, while tailored to withstand particular environmental factors, can vary in their susceptibility to compression set. For example, silicone rubber is known for its stability across a wide temperature range and is less prone to compression set in high-temperature applications. On the other hand, nitrile rubber, though excellent in oil-resistant applications, may exhibit a higher compression set when exposed to sustained compressive forces over time. The choice of material must, therefore, align with both the environmental conditions and the performance requirements of the application to minimise compression set effectively.
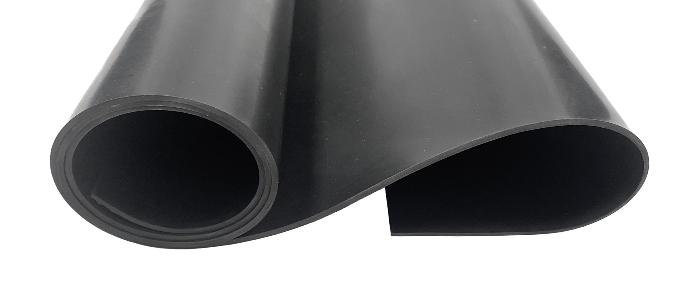
The formulation of the rubber compound, including the type and amount of fillers, plasticisers and curing agents can also play a role in determining compression set. Compounds with higher levels of fillers or plasticisers may have lower resilience and thus a higher compression set, while those that are properly cured and cross-linked tend to perform better in terms of maintaining their shape under compression.
Level and Duration of Compression
The level of compression applied to a rubber seal is also a factor in determining its compression set. When a seal is compressed within its optimal range, it effectively deforms to fill the gap and create a tight seal between surfaces. However, if the seal is compressed beyond this range, the internal structure of the rubber, which consists of interconnected polymer chains, can become overstressed. This overstressing can lead to the breakdown of these chains or cause them to reorient in a way that hinders their ability to return to their original shape. As a result, the rubber becomes more prone to permanent deformation, increasing its compression set and reducing its effectiveness over time.
The duration for which a rubber seal remains under compression also influences its compression set. Even if a seal is compressed within its ideal range, prolonged compression can still lead to permanent deformation. Rubber is a viscoelastic material, meaning it exhibits both elastic and viscous behaviour. Over time, the viscous nature of the rubber allows it to creep, or slowly flow, under sustained pressure. This creeping effect causes the material to deform gradually, and when the compressive force is finally removed, the rubber may not fully recover its original shape. The longer the duration of compression, the more pronounced this effect becomes, leading to a higher compression set.
In practical applications, both the level and duration of compression must be carefully managed to minimise compression set and ensure the long-term reliability of rubber seals. Engineers and designers need to account for these factors during the design and material selection processes to ensure that seals are not only appropriate for the initial conditions but also capable of maintaining their performance over time. This consideration is especially important in applications where seals are expected to remain in place for extended periods without being released from compression. This can result in significant performance degradation if the compression set is not adequately controlled.
Temperature and Environmental Conditions
Temperature also plays an influencing factor in determining the compression set of rubber seals. It can significantly affect the materials properties and its ability to return to its original shape after compression. At higher temperatures, rubber tends to soften, which can increase its susceptibility to permanent deformation. The elevated heat causes the rubbers polymer chains to become more flexible and allow the material to flow more easily into the gaps and irregularities of the surface it is sealing. While this might enhance the initial sealing performance, it also makes the rubber more prone to taking on a permanent set. This is because the material would struggle to recover fully once the compressive force is removed. Consequently, rubber seals operating in high-temperature environments often exhibit a higher compression set, which can compromise their long-term effectiveness.
Low temperatures can also influence compression set, though in a different manner. At very low temperatures, certain rubber compounds can become brittle and lose their elasticity. This can result in a lack of ability to bounce back after being compressed. This brittleness can lead to cracking or other forms of material failure which would further contribute to a higher compression set. The reduced flexibility at low temperatures can also prevent the rubber from forming a proper seal in the first place, as the material may not adequately conform to the surfaces it is intended to seal.
Beyond temperature, various environmental conditions can further impact the compression set of rubber seals. Exposure to chemicals, oils, ozone or UV radiation can cause the rubber material to degrade, either by swelling, hardening or cracking. For example, rubber seals that come into contact with certain oils or solvents may experience swelling which would alter their dimensions and make them more prone to permanent deformation. Similarly, prolonged exposure to UV radiation or ozone can lead to surface hardening and cracks. This would reduce the materials ability to recover after compression. These environmental stresses can significantly contribute to an increased compression set and ultimately affect the seals long term performance and reliability.
The Impact of Compression Set on Seal Performance
Compression set has a direct impact on the performance and reliability of a rubber seal. A seal that has experienced significant compression set may no longer be able to provide an effective barrier and experience leaks that could potentially compromise the entire system. This is especially important in applications where maintaining a tight seal is essential for safety, efficiency or the prevention of contamination.
For example, in automotive applications, rubber seals are used in engines, transmissions and braking systems to prevent the leakage of fluids like oil, coolant or brake fluid. If these seals develop a high compression set, they may no longer fit snugly against the surfaces they are meant to seal and result in fluid leaks that could cause engine damage, decreased braking performance or even complete system failure.
In industrial settings, rubber seals are often used in hydraulic systems, pumps and valves. A high compression set in these seals can lead to pressure loss, reduced efficiency and increased maintenance costs. In extreme cases, this can cause equipment failure, costly downtime and potential safety hazards.
Even in everyday applications, such as household plumbing, the compression set of rubber seals is important. A deformed seal in a tap or pipe joint can result in water leaks, leading to water damage, increased water bills and the need for repairs or replacements.
Minimising Compression Set in Rubber Seals
While it is impossible to eliminate compression set entirely, several strategies can be adopted to minimise its impact and ensure that rubber seals perform effectively over their intended lifespan.
Material Selection
Choosing the right rubber material for the specific application helps minimise compression set. Materials should be selected based on their ability to withstand the operating conditions, including temperature, pressure and exposure to chemicals or other environmental factors. For example, silicone rubber is often chosen for high-temperature applications due to its excellent heat resistance and low compression set characteristics, while EPDM is favoured in environments where exposure to ozone or UV radiation is a concern.
Working closely with material suppliers and engineers can help identify the best rubber compound for a given application and ensure that the seal performs well under the expected conditions. This minimises the risk of compression set.
Optimal Seal Design
The design of the seal itself can also play a role in reducing compression set. Seals should be designed to operate within their optimal compression range and avoid excessive compression that could lead to permanent deformation. Additionally, the use of seals with larger cross-sectional areas can distribute the compressive force more evenly and reduce the stress on any one part of the seal.
In some cases, it may also be beneficial to use seals with a built-in recovery feature, such as a spring or metal insert, which helps the seal maintain its shape and function even after prolonged compression.
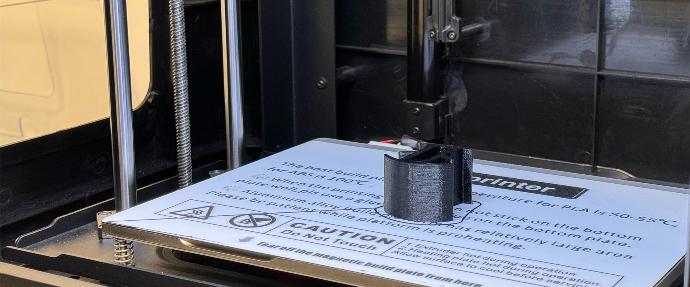
Controlling Operating Conditions
Where possible, controlling the operating conditions can help reduce the impact of compression set. This includes maintaining temperatures within the recommended range for the chosen rubber material and avoiding prolonged exposure to chemicals, oils or other substances that could degrade the rubber. Regular maintenance and inspection of seals can also help identify early signs of compression set, allowing for timely replacement before the seal's performance is compromised.
Using Lubricants and Additives
The application of appropriate lubricants or the incorporation of additives into the rubber compound can also help reduce compression set. Lubricants can reduce friction and wear, allowing the seal to return to its original shape more easily after compression. Similarly, additives that improve the elasticity and resilience of the rubber can help maintain its shape under pressure, reducing the likelihood of permanent deformation.
Minimising Compression Set in Rubber Seals
Compression set is an important factor in the performance and longevity of rubber seals. By understanding the causes of compression set and employing strategies to minimise its impact, it is possible to enhance the effectiveness of seals in a wide range of applications. Whether through careful material selection, optimised seal design, controlled operating conditions or the use of lubricants and additives, addressing compression set helps ensure that rubber seals provide long-lasting performance. This, in turn, helps maintain the integrity of the systems they are used in, whether in automotive, industrial, household or other settings.
Seals Direct is a leading manufacturer and supplier of rubber seals, trims and associated products. Our experienced team is able to advise on the best product and material for your application, that takes into account any compression required of the rubber profile. Please give us a call on 01425 617722 or contact us by email at sales@sealsplusdirect.co.uk.