Rubber seals are important to many industries, from automotive to plumbing and aerospace. Their primary function is to prevent the leakage of fluids, gases or other substances by creating a tight seal between two surfaces. However, one of the challenges often encountered with rubber seals is a phenomenon known as "stiction". This term, a blend of "static" and "friction", refers to the resistance to the start of motion that can occur when a rubber seal adheres too strongly to the surface it is supposed to seal. Understanding what causes stiction is important in the selection, application or maintenance of rubber seals.
What is Stiction?
Stiction, in the context of rubber seals, is the force required to initiate movement between the seal and the surface it is in contact with. When a rubber seal is at rest against a surface, the materials can bond slightly at a microscopic level due to factors such as molecular adhesion and the settling of the seal material. When movement is required, this initial bond must be broken. The force needed to overcome this bond is what we refer to as stiction.
This restriction is particularly important in applications where precision and smooth motion are required. High stiction can lead to jerky or uneven movement which may cause problems in applications such as the opening and closing of windows. In some cases, excessive stiction can even lead to damage to the seal or the surface it contacts and reduce the overall effectiveness of the seal.
Causes of Stiction in Rubber Seals
Stiction in rubber seals can be a complicated issue influenced by multiple factors that each contribute to the resistance encountered when initiating movement between the seal and the surface it contacts. Understanding these causes helps those who design, select or maintain sealing systems, as addressing them can significantly improve performance and longevity. The primary factors contributing to stiction include the material properties of the rubber seal, the surface characteristics of the sealed area, environmental conditions and the duration of contact between the seal and the surface.
Material Properties
The material composition of the rubber seal is the most important factors in determining the level of stiction. Rubber compounds vary widely in their properties, including hardness, elasticity and adhesion. For instance, softer rubber materials tend to deform more under pressure. This increases the contact area with the surface and the potential for stiction. This increased contact area allows more points of microscopic adhesion to develop between the rubber and the surface resulting in a higher resistance when movement is initiated.
The opposite can be said for harder rubber materials that deform less and provide a smaller contact area. However, these harder materials may also be less effective at sealing, especially in applications where flexibility and conformity to surface irregularities is important. The trade-off between hardness and sealing effectiveness must be carefully considered to manage stiction effectively.
The chemical composition of the rubber can also affects its interaction with the surface. Some rubber compounds are more prone to developing strong molecular adhesion with certain materials, especially metals. For example, nitrile rubber (NBR) is known for its excellent resistance to oils and fuels but can exhibit higher stiction in certain applications due to its adhesion properties. Silicone rubber is known for its low surface energy and often exhibits lower stiction but may not provide the necessary sealing performance in all environments.
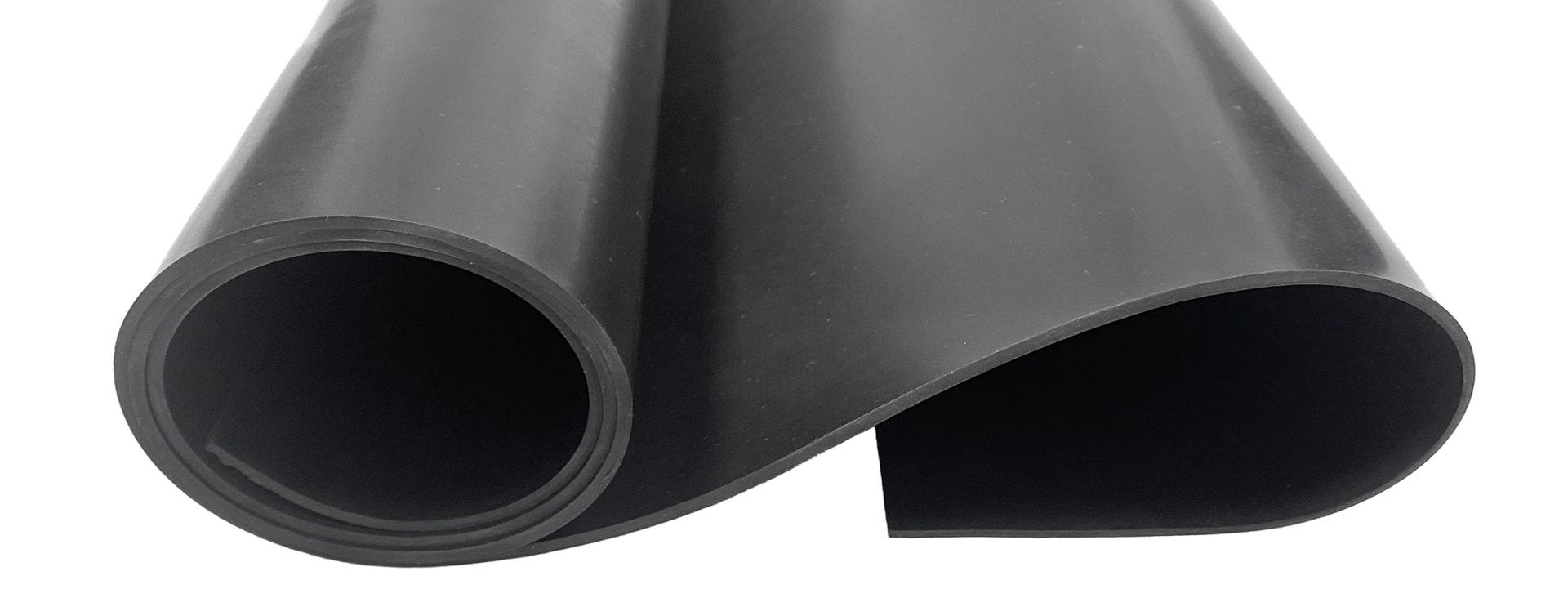
Surface Characteristics
The characteristics of the surface against which the rubber seal is pressed is another major factor that can influence stiction. Surface roughness plays a significant role in this context. Very smooth surfaces can increase stiction because it maximises the area of contact between the rubber and the surface. This large surface contact increases molecular adhesion. When the rubber material conforms closely to a smooth surface, more points of contact are established which result in a higher resistance when the seal is required to move.
Rougher surfaces can reduce stiction by decreasing the contact area as the rubber may not fully conform to the irregularities of the surface. However, if the surface is too rough, it can compromise the effectiveness of the seal. The rubber might not fill in all the gaps and cause potential leakage. Rough surfaces can also damage softer rubber materials, such as sponge rubber and silicone. Finding an optimal surface finish that balances sealing performance with minimal stiction is key in many applications.
Another surface-related factor is the presence of coatings or treatments. Surfaces that have been treated with anti-stick coatings, such as PTFE (polytetrafluoroethylene), can reduce the adhesion between the rubber and the surface. This would lower stiction. However, these coatings must be compatible with the rubber material and the operating conditions of the application to be effective.
Environmental Conditions
Environmental factors such as temperature, humidity and the presence of lubricants significantly influence stiction in rubber seals. Temperature, in particular, can have an effect on the physical properties of rubber. At higher temperatures, rubber tends to soften, which can increase its adhesion to the surface. This is because the softened rubber can more easily flow into surface irregularities and increase the contact area. At lower temperatures, rubber can become stiffer and less flexible, which may reduce its ability to conform to the surface but can also make it more difficult to initiate movement due to reduced elasticity.
Humidity, especially in cases where the rubber material is hygroscopic or when water acts as a lubricant or adhesive, can also play a role. High humidity can lead to the absorption of moisture by the rubber which could alter its properties and increase stiction. Additionally, in some cases, water can form a thin film between the seal and the surface which, depending on other factors and conditions, may either increase or decrease this friction.
Lubricants are another environmental factor. The
presence of lubricants, such as oils or greases, can significantly reduce stiction
by providing a barrier between the rubber and the surface. However, the
effectiveness of a lubricant depends on its compatibility with both the rubber
material and the operating environment. For example, certain lubricants may
cause rubber to swell or degrade over time. Careful selection of lubricants is
essential to balance the reduction of sticking and friction with the long-term
integrity of the seal.
Duration of Contact
The duration for which the rubber seal remains in contact with the surface also affect how it moves. Over time, the rubber material can undergo physical changes, such as creep or compression set, which is the deformation of the material under stress. As the rubber creeps, it can flow into microscopic surface irregularities and increase the contact area. Additionally, prolonged contact can lead to the development of stronger molecular bonds between the rubber and the surface, making it more difficult to initiate movement.
Chemical changes can also occur over time, particularly in environments where the seal is exposed to reactive substances, UV light, or ozone. These conditions can cause the rubber to harden or degrade, altering its adhesion properties and potentially increasing stiction. For instance, oxidation of the rubber surface can create a sticky layer that enhances adhesion to the sealed surface.
In applications where seals are expected to remain stationary for long periods, such as in storage or infrequently used machinery, the buildup of stiction can be particularly pronounced. When the time comes to activate these seals, the force required to overcome the stiction can be significantly higher than anticipated, potentially leading to sudden movements, system shocks, or even damage to the seal or the components it interacts with.
The Impact of Stiction on Seal Performance
Stiction in rubber seals can significantly impact the performance and reliability of mechanical systems. One of the most immediate effects is the introduction of jerky or uneven movement, often referred to as stick-slip behaviour. This occurs when the initial resistance due to stiction is suddenly overcome causing abrupt movements rather than a smooth controlled motion. Such erratic behaviour is particularly problematic in systems where precision is necessary, such as hydraulic actuators, automotive steering mechanisms and aerospace control surfaces. Stick-slip in this instances could reduce performance and compromise safety.
Beyond affecting movement, stiction also contributes to increased wear and tear on both the rubber seal and the surfaces it contacts. The higher forces needed to initiate movement under stiction can cause micro-tears or abrasions on the seal. This would gradually degrade its integrity causing leaks or premature failure. Additionally, the surfaces that come into contact with the seal may suffer from scratches or pitting due to the sudden release of frictional forces. This necessitates more frequent maintenance or component replacements which increases operational costs.
Stiction also has implications for energy efficiency. Systems burdened by stiction require more force and energy to initiate movement. This increased energy demand can reduce overall system efficiency, particularly in energy-sensitive applications such as electric vehicles or industrial machinery. The additional strain placed on components can lead to overheating, fluid degradation and potential system failures.
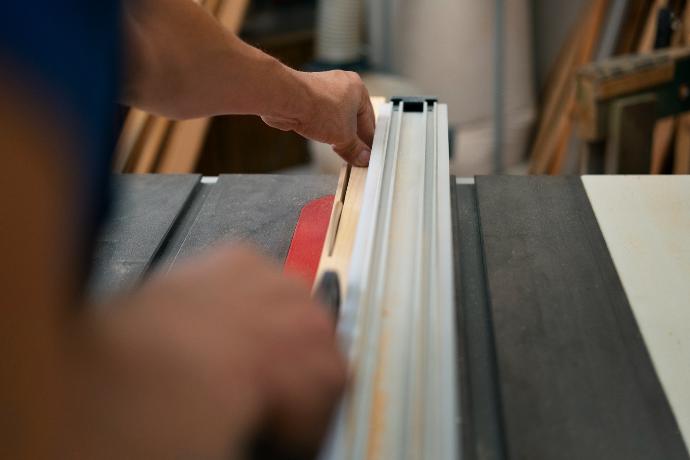
Minimising Stiction in Rubber Seals
Minimising stiction in rubber seals helps ensure the smooth operation, reliability and longevity of mechanical systems. Although stiction cannot be entirely eliminated, there are several ways to reduce its effects and enhancing the overall performance of the seal and the system it serves. These strategies include careful material selection, surface treatment, lubrication and optimised seal design.
Material Selection
One of the most effective ways to minimise stiction is through the careful selection of rubber materials. Different rubber compounds have varying degrees of adhesion, elasticity and hardness,. For example, materials like silicone rubber or fluoroelastomers are often preferred in applications where low stiction is important due to their lower inherent adhesion properties. These materials offer the necessary flexibility and durability while reducing the tendency to adhere too strongly to surfaces. However, it is essential to balance these properties with the specific environmental conditions and performance requirements of the application to ensure that the chosen material not only reduces stiction but also meets other performance criteria.
Surface Treatment
Surface treatment is another key strategy. Modifying the surface of the sealed area can significantly influence the interaction between the seal and the surface. For example, polishing the surface to reduce roughness or applying anti-stick coatings like PTFE (polytetrafluoroethylene) can decrease the contact area and adhesion forces between the rubber and the surface. This reduction in contact and adhesion directly translates to lower stiction and allows for smoother and more predictable movement of the seal.
Lubrication
Lubrication is perhaps the most commonly used method to combat stiction. The application of appropriate lubricants creates a thin barrier between the seal and the surface to reduce friction and the tendency for the materials to adhere. Silicone-based or PTFE lubricants are widely used because they are compatible with many rubber compounds and provide a long-lasting solution for reducing stiction. However, it is important to select lubricants that are compatible with the seal material and the operating environment. Incompatible lubricants can cause swelling, degradation or other adverse effects on the seal. This could ultimately lead to increased stiction or seal failure.
Seal Design
The design of the seal itself can also be optimised to minimise stiction. Seals with a reduced contact area, such as those featuring a lip design, can lower the forces required to initiate movement by decreasing the amount of rubber in contact with the surface. Additionally, ensuring that seals are not excessively compressed in their housings can prevent them from adhering too strongly to the surface, further reducing stiction. In some cases, the incorporation of grooves or other design features can help to distribute the contact forces more evenly, reducing the likelihood of stiction occurring.
It is also possible purchase some rubber seals with a flocked coating. This is velvet-like texture that reduces friction between the two surfaces. It is commonly used on window seals in cars where the glass panel needs to easily glide in the window frame.
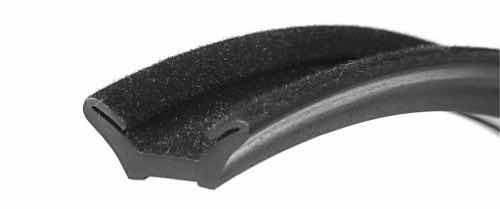
Purchase the Correct Rubber Seal From Seals Direct
Stiction is an important consideration in the use of rubber seals particularly in applications that require precise and smooth motion. By understanding the causes of stiction and employing strategies to minimise its effects, it is possible to enhance the performance and longevity of rubber seals in a wide range of applications. Material selection, surface treatment, lubrication and careful design should all be considered in managing stiction and ensuring that seals perform as expected.
Seals Direct is a leading manufacturer and supplier of rubber seals, trims and associated products. Our experienced team is able to advice on the best product and material for your application, that takes into account any movement required of the rubber profile. Please give us a call on 01425 617722 or contact us by email at sales@sealsplusdirect.co.uk.