Rubber seals are important for many applications, from sealing windows in caravans to protecting sensitive equipment in industrial settings. These seals are made from various types of rubber, each selected for its specific properties to suit the demands and requirements of the final application. One of the most important factors in determining which rubber material is appropriate for a seal is its hardness. The hardness of rubber is measured on the Shore scale, a system that helps manufacturers identify and choose an appropriate hardness. But what does this hardness actually mean, and how does it affect the performance of a rubber seal?
This article from Seals Direct explores Shore hardness in rubber seals with a particular focus on two specific types of rubber. Sponge rubber, measured on the Shore OO scale, and solid rubber, measured on the Shore A scale. These two types of rubber seals are commonly used in different applications, and understanding their hardness helps in choosing the right seal for each situation.
What is Shore Hardness?
Shore hardness is a way of measuring the hardness of a material, particularly how resistant it is to indentation. This concept was introduced by Albert Ferdinand Shore in the early 20th century and has since become a standard in the industry. The Shore hardness of a material is determined by pressing a specific type of indenter into the material and measuring how much it penetrates. The result is a numerical value on the Shore scale, with higher numbers indicating harder materials.
There are several different Shore scales, each designed to measure the hardness of different types of materials. For rubber seals, the most commonly used scales are Shore A and Shore OO. Shore A is typically used for harder materials like solid rubber, while Shore OO is used for softer more compressible materials like sponge rubber. These scales help manufacturers and end users choose the right type of rubber for specific sealing applications. This ensures that the seal will perform as expected under the conditions it will face.
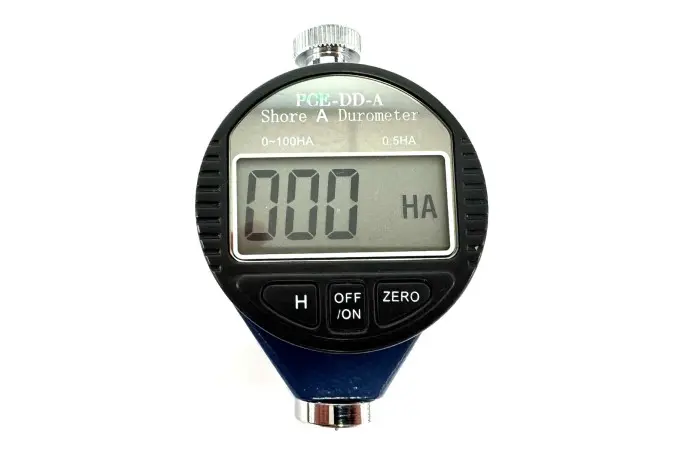
Understanding Sponge Rubber and Shore OO Hardness
Sponge rubber is a type of rubber characterised by its cellular structure that is often soft and compressible. This structure allows sponge rubber seals to compress easily under pressure. This is an important characteristic for applications where a more flexible seal is required. The softness of sponge rubber is measured on the Shore OO scale, which is specifically designed for materials that are too soft to be accurately measured on the Shore A scale.
The Shore OO scale ranges from 0 to 100 with lower numbers indicating softer materials. Sponge rubber typically falls within the lower to mid-range of this scale, depending on its formulation. A Shore OO hardness of 20, for example, would indicate a very soft sponge rubber, while a hardness of 50 would be firmer but still much softer than most solid rubbers.
To better understand different hardnesses, they are often compared to everyday objects.
- Shore 10 OO is comparable to a soft jelly sweet
- Shore 30 OO is comparable to a gel shoe insert
- Shore 60 OO is comparable to an elastic band
- Shore 80 OO is comparable to a pencil eraser
The softness of sponge rubber makes it suitable for applications where a reliable seal is required. For example, it is often used in seals for doors and windows, where it needs to compress easily to create an effective barrier against air and water. Because sponge rubber can conform to irregular surfaces, it is also used in applications where the sealing surface may not be perfectly smooth or where there is a need to fill gaps. However, its softness also means that it is not as durable as harder rubbers and may not be suitable for applications where the seal will be subjected to high pressure or wear.
Understanding Solid Rubber and Shore A Hardness
Solid rubber is much denser and less compressible than sponge rubber. This type of rubber is commonly used in applications where a strong and hardwearing seal is required. The hardness of solid rubber is measured on the Shore A scale, which is the most widely used scale for rubber materials. Shore A hardness values also range from 0 to 100, with higher numbers indicating harder materials.
Solid rubber used in seals typically has a Shore A hardness between 40 and 90, depending on the specific application. For example, a rubber seal with a Shore A hardness of 40 would be relatively soft and flexible. This is often suitable for applications where some flexibility is needed but where the seal still needs to withstand moderate pressure. A Shore A hardness of 70 or 80, on the other hand, would indicate a much harder rubber. This hardness is often appropriate for applications where the seal needs to resist significant pressure or where durability is more important than flexibility.
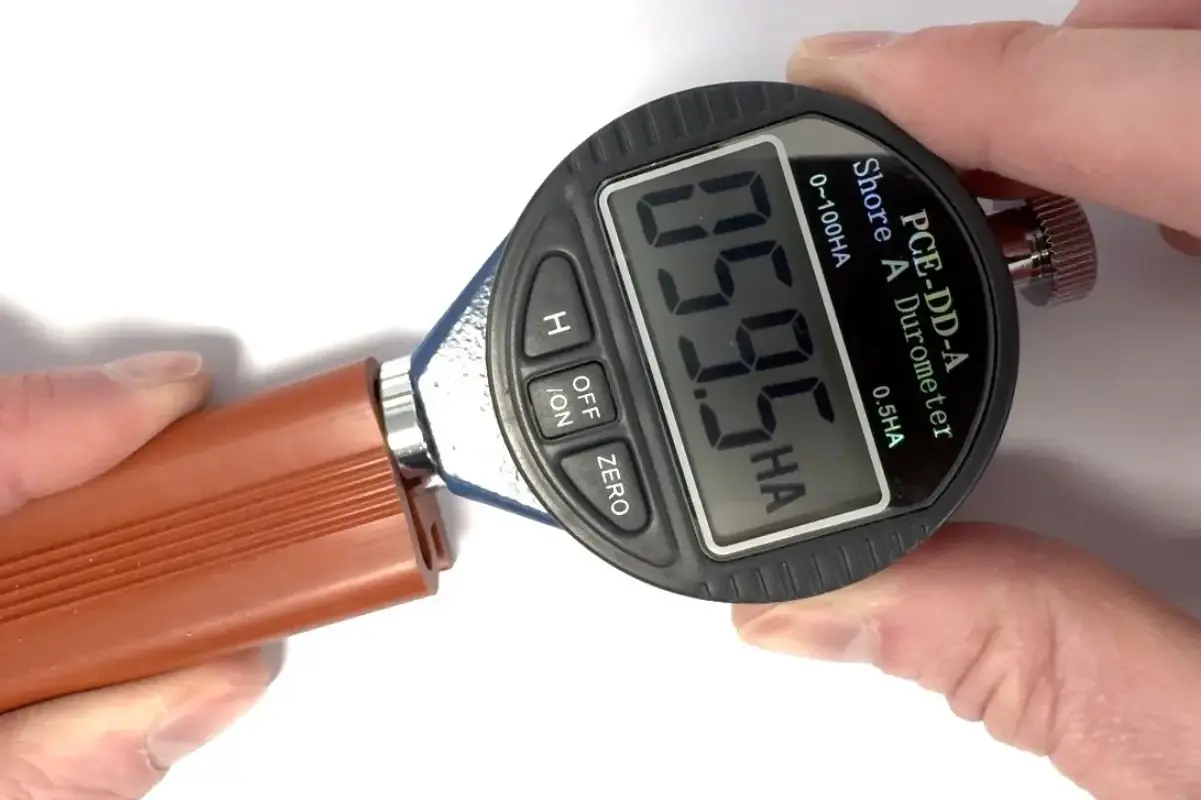
To better understand different hardnesses, they are often compared to everyday objects.
- Shore 20 A is comparable to an elastic band
- Shore 40 A is comparable to an inner tube
- Shore 50 A is comparable to a pencil eraser
- Shore 60 A is comparable to the rubber on a car tyre
- Shore 70 A is comparable to shoe sole
- Shore 80 A is comparable to a leather belt
The Shore A hardness of solid rubber makes it
ideal for applications where the seal needs to maintain its shape and integrity
under stress. This includes uses such as gaskets in engines, where the rubber
needs to withstand high temperatures and pressures without deforming. Solid
rubber seals are also used in industrial machinery, where they need to resist
wear and tear over long periods. However, the hardness of solid rubber means
that it is less able to conform to uneven surfaces than sponge rubber, so it
may not be suitable for applications where the sealing surface needs to create
a fully watertight seal.
How to Measure Shore Hardness
Measuring Shore hardness is a fairly straightforward process but requires the correct equipment and proper technique to ensure accurate results. The measurement is conducted using a device known as a durometer, which is specifically designed to test the hardness of materials like rubber, plastic and other polymers. The durometer consists of a calibrated spring and an indenter, which is a small pointed probe that presses into the material being tested.
To measure the Shore hardness of a rubber seal, you would follow these steps:
1. Prepare the Sample: Ensure that the rubber sample is at least 6mm thick. If the material is thinner, you can stack layers to achieve the required thickness, as long as the layers are tightly bonded together. The sample should have a smooth, flat surface to get an accurate reading.
2. Position the Durometer: Place the durometer on the surface of the rubber sample. The device should be perpendicular to the surface to ensure that the indenter presses straight into the material. It is important that the durometer is held steadily during the measurement to avoid skewing the results.
3. Apply the Pressure: Gently apply pressure to the durometer so that the indenter penetrates the surface of the rubber. The indenter will push into the material, and the durometer will measure how much the material resists this indentation. For Shore A measurements, the indenter is usually a truncated cone, while for Shore OO measurements, the indenter is spherical.
4. Read the Measurement: Once the indenter has been pressed into the rubber for a set amount of time (typically about one second), the durometer will display a reading on a scale from 0 to 100. This number represents the Shore hardness of the material. A higher number indicates a harder material, while a lower number indicates a softer material.
5. Repeat the Measurement: To ensure accuracy, it is advisable to take multiple measurements at different points on the rubber sample. The final Shore hardness value is usually the average of these measurements.
Several factors can affect the accuracy of a Shore hardness measurement. These include the thickness of the sample, the temperature at which the test is conducted and the consistency of the material. For example, rubber becomes softer at higher temperatures, which could result in a lower Shore hardness reading if the test is conducted in a warmer environment.
It is also important to ensure that the durometer is properly calibrated before use. An uncalibrated device may give inaccurate readings, which could lead to incorrect conclusions about the hardness of the material. Regular calibration checks are essential, particularly in industrial settings where precise measurements are important.
Comparing Sponge Rubber and Solid Rubber
When comparing sponge rubber and solid rubber, it is best to understand how their different Shore hardnesses affect their performance in various applications. Sponge rubber, with its lower Shore OO hardness, is much softer and more compressible than solid rubber. This makes it ideal for applications where a flexible or compressible seal is required, particularly in environments where the sealing surfaces may be irregular or where a certain amount of cushioning is required.
Solid rubber, with its higher Shore A hardness, is much harder and more durable. It is better suited to applications where the seal needs to withstand high pressures or where it will be exposed to harsh conditions, such as extreme temperatures or chemicals. However, its hardness means that it is less flexible than sponge rubber and may not create as effective a seal on uneven surfaces.
The choice between sponge rubber and solid rubber will depend on the specific requirements of the application. For example, with caravan door seals, where the surface may not be perfectly even and where the seal needs to compress to prevent air and water from entering, sponge rubber with a mid-range Shore OO hardness may be the better choice. This compares to a seal in an engine, where the seal needs to withstand high pressures and temperatures, solid rubber with a higher Shore A hardness would be more appropriate.
Choose the Right Rubber Seal with Seals Direct
When selecting a rubber seal, it is important to consider the Shore hardness of the material, as this will affect how the seal performs in its intended application. A seal that is too soft may not provide enough resistance and result in leaks or other issues. Whilst a seal that is too hard may not conform properly to the surfaces it is intended to seal.
Sponge rubber seals, with their low Shore OO hardness, are ideal for applications where flexibility and compressibility are key, such as in door seals, window seals and other applications where a gentle seal is required. Solid rubber seals, with their higher Shore A hardness, are better suited to applications where durability and resistance to pressure are more important, such as in gaskets, industrial machinery, and other demanding environments.
By understanding the differences between Shore OO and Shore A hardnesses, you can make an informed decision about which type of rubber seal is best suited to your needs. Whether you need a soft, flexible seal or a hard, durable one, the right rubber material will ensure that your seals perform effectively and reliably in their intended application.
Seals Direct is a leading manufacturer and supplier of rubber seals, trims and gaskets. Our experienced team is able to advice on the best Shore hardness for your application. Please give us a call on 01425 617722 or contact us by email at sales@sealsplusdirect.co.uk.