What is Sponge Rubber?
Sponge rubber is a type of rubber known for its open-cell or closed-cell structure. These variants are categorically different as open-cell sponge allows air and liquids to pass through the cellular structure, whereas closed-cell sponge is impermeable to air and water. The specific properties of sponge rubber, like density and elasticity, can be adjusted during manufacturing to suit the required application.
The cellular nature of both open-cell and closed-cell sponge rubber demonstrates a unique set of properties that makes it suitable for automotive, marine and industrial sealing applications. It finds extensive use in various situations where cushioning, sealing and insulation are required.
Sponge rubber is available in various forms, such as extruded sponge profiles, cut strip and large sheets. These products are available with or without a self-adhesive backing.
What is Solid Rubber?
Solid rubber is a dense non-porous rubber that does not have a cellular structure. This gives it a higher tensile strength and resistance to ware. Solid rubber can be formulated with different levels of hardness, elasticity and resistance to various environmental factors like temperature, chemicals, and UV light.
The versatility of solid rubber makes it a crucial material commonly used in a wide range of industries that require toughness and resistance to deformation under pressure. Solid rubber in sealing applications is commonly used for edge protection, sealing windows and cushioning heavy machinery.
Solid rubber is available in a large selection of forms, such as extruded solid profiles and cut rubber strip.
What Is The Difference Between Sponge And Solid Rubber?
The difference between sponge rubber and solid rubber lies in their structure, manufacturing processes, applications and characteristics.
Composition and Structure
Sponge rubber has a cellular structure that gives it a compressible cushion-like quality. This compares to solid rubber which is dense and non-porous. It lacks the cellular structure of sponge rubber, resulting in a rigid sturdy material. This also gives it higher tensile strength and durability.
Manufacturing Process
There is also a distinctive difference between the processes used to manufacture sponge and solid rubber products. Sponge rubber is produced by incorporating nucleating agents, such as nitrogen or carbon dioxide, into the rubber compound. During curing, these agents decompose and create gas bubbles within the rubber that forms the cellular structure. The nature of these cells, whether open or closed, depends on the curing method and the specific formulation of the rubber compound.
Solid rubber is made without a nucleating agent, resulting in a compact non-porous material.
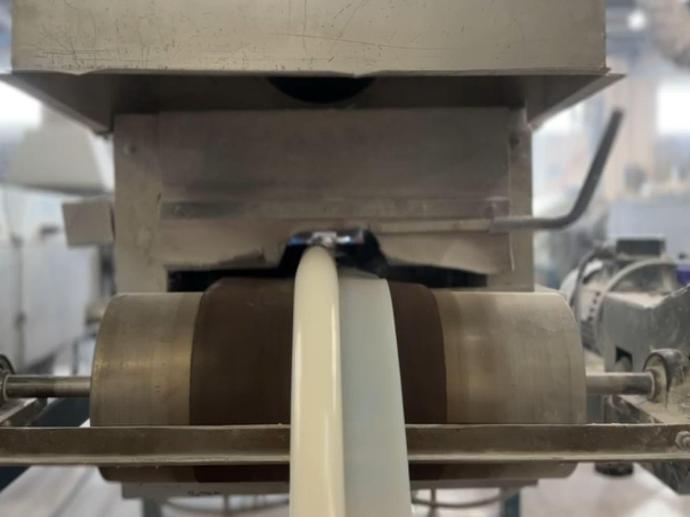
Properties and Characteristics
Due to their structural differences, sponge and solid rubber have distinct physical properties. Sponge rubber is known for its compressibility, flexibility and cushioning. The cellular structure also provides good thermal and sound insulation properties. However, it generally has a lower tensile strength and tear resistance compared to solid rubber.
Solid rubber is valued for its strength, durability and resistance to abrasion. It is less compressible than sponge rubber and does not provide the same level of cushioning or insulation. Solid rubber performs well in applications requiring resistance to wear and tear and is capable of withstanding higher pressures.
Applications
The applications of sponge and solid rubber are influenced by their properties. Sponge rubber is commonly used in sealing applications, such as gaskets and weather stripping, where compressibility and cushioning is essential to create a watertight seal. It is also commonly used for insulation, such as in thermal or acoustic padding.
Solid rubber is desirable in areas where strength, durability and resistance to wear is essential. This includes tyres, conveyor belts and industrial rollers. Its ability to withstand higher pressures and wear makes it suitable for more demanding applications.
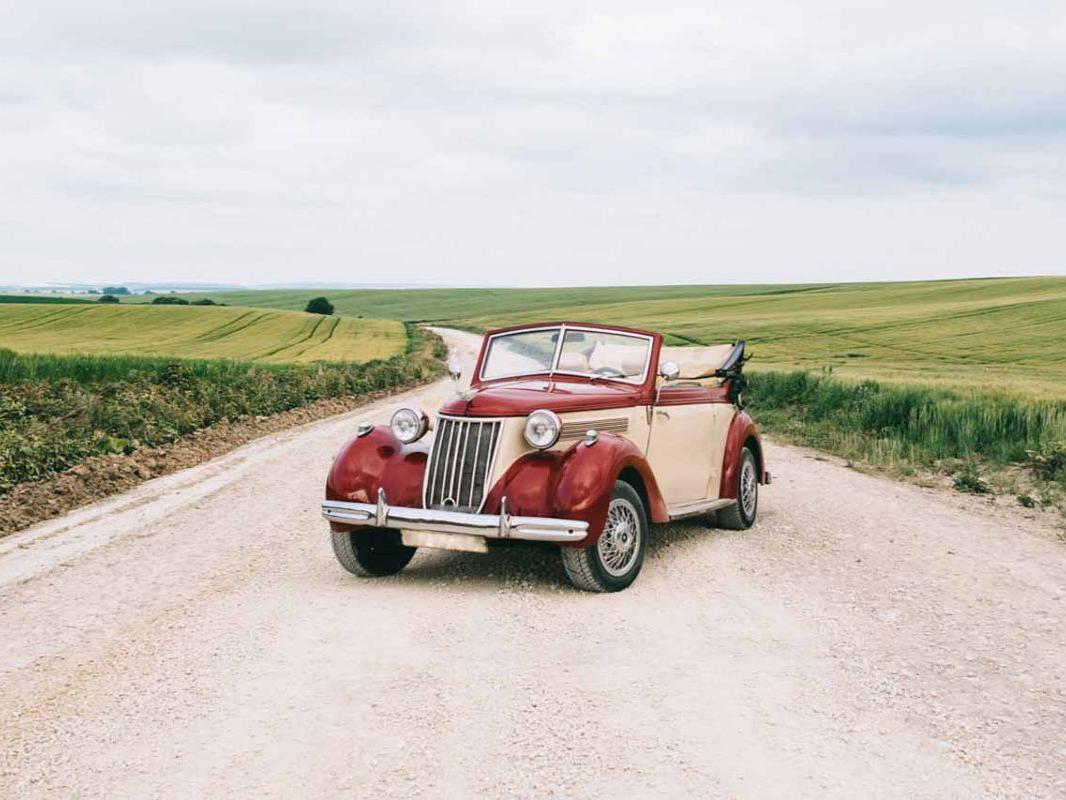
Environmental and Chemical Resistance
The resistance of sponge and solid rubber to environmental factors and chemicals is heavily dependent on the underlying rubber compound. Sponge rubber, especially the open-cell type, is more susceptible to water absorption and may not perform well in wet conditions. Closed-cell sponge rubber offers better water resistance but may still be vulnerable to certain chemicals and oils.
Depending on the chosen compound, solid rubber typically has better resistance to water, oils and many chemicals. This makes it more suitable for use in harsher environments where exposure to such elements is likely.
Maintenance and Longevity
In terms of maintenance and longevity, solid rubber generally requires less maintenance and lasts longer than sponge rubber. The cellular structure of sponge rubber can lead to the breakdown of the section, especially in harsh environments. Solid rubber, being more robust and less prone to environmental damage, tends to have a longer lifespan under similar conditions.
Should I Use Sponge Rubber or Solid Rubber?
Sponge and solid rubber are distinct materials with different structures, manufacturing processes, properties and applications. Sponge rubber, with its cellular structure, offers compressibility and insulation but lacks the strength and durability of solid rubber. As solid rubber is dense and non-porous, it excels in strength, durability and resistance to wear. This makes it suitable for more demanding applications.
The choice between whether you should use sponge or solid rubber depends on the specific requirements of the project. You should take time to consider factors such as the environment it will be used in, the required life span and the budget.
With an extensive selection of sponge rubber, solid rubber and rubber extrusions available, it is possible to choose a product most suitable for the chosen application. Please contact our helpful team if you require technical help and support in deciding on the best product.