3D printing technology has significantly transformed the manufacturing and prototyping landscape, especially within the rubber industry. One of the most innovative advancements in this domain is the use of flexible 3D printer filaments, particularly those made from Thermoplastic Polyurethane (TPU). As these filaments closely mimic the properties of rubber, they are an ideal material for prototyping rubber seals. This minimises the requirement for expensive and time consuming tooling that is often associated with prototyping products using other rubber materials.
This article explores the benefits and applications of using flexible filaments to prototype rubber seals. We will also look at an example of how this process has been used to help one of our long-standing customers.
What is a Flexible TPU Filament?
In simple terms Thermoplastic Polyurethane (TPU) is a blend of rubber and PVC. It is a versatile material known for its elasticity, durability and resistance to abrasion, chemicals and oils. These characteristics make TPU an excellent substitute for rubber in various applications. This material is commonly used within the sealing industry to manufacture glazing gaskets for uPVC windows and doors.
TPU filaments used in 3D printing are usually flexible. They are commonly used to print flexible products that closely resemble the hardness and properties of traditional rubber seals. It offers the necessary flexibility to create rubber-like seals that can stretch and return to their original shape without deformation. This property is important for applications where the seal must maintain a tight fit under varying pressures and movements. As TPU is known for its durability and resistance to wear and tear, this also allows prototyped seals to withstand repeated use and environmental factors to allow for thorough testing and validation before mass production.
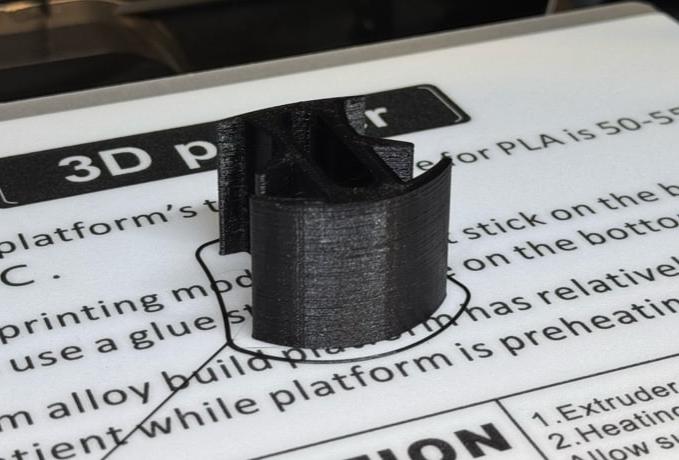
At Seals Direct, we use TPU-95A which is a type of TPU that has a 95 Shore hardness. This material provides all the benefits of TPU with a high elasticity that is easy to print and offers excellent layer-to-layer bonding. Our TPU-95A filament is available in a large selection of colours including black, grey, white, blue, green, orange, red, pink, yellow and purple.
Advantages of Prototyping Over Traditional Tooling
Prototyping rubber seals using a flexible filament offers several advantages over traditional tooling and longer production runs associated with using other rubber materials. One of the primary benefits is cost efficiency. Traditional tooling involves creating a die which usually costs between £150 and £400, depending on the complexity of the profile. For small prototype runs, the cost of this tooling can be prohibitively high. This compares to 3D printing which completely eliminates the need for the development of any tool. This significantly reduces initial setup costs.
Another advantage is the speed of production. Traditional manufacturing methods often require weeks or even months to produce and refine the initial tool. However, a 3D printed prototype allows for rapid prototyping. This enables designers to produce and test multiple profiles in a matter of days. This accelerated timeline is often important for quickly refining designs and developing sealing solutions suitable for the final application.
The flexibility and ease of customisation offered by 3D printing with TPU are also significant benefits. Traditional rubber manufacturing processes are less adaptable to design changes once the initial tool has been created. Any modifications to the design often require a new tool which adds to the time and cost. As 3D printing does not require any tooling, it allows for easy adjustments to the digital model.
Case Study: Rapid Prototyping Rubber Seals
We were approached by a long-standing customer who was looking for a custom rubber sealing solution. They were looking for a bespoke section that could be inserted between roofing panels to minimise the amount of water that entered the outbuilding. Although the final product would require tooling and production using a rubber material such as EPDM, they were being pressed for time from their client to demonstrate a working solution.
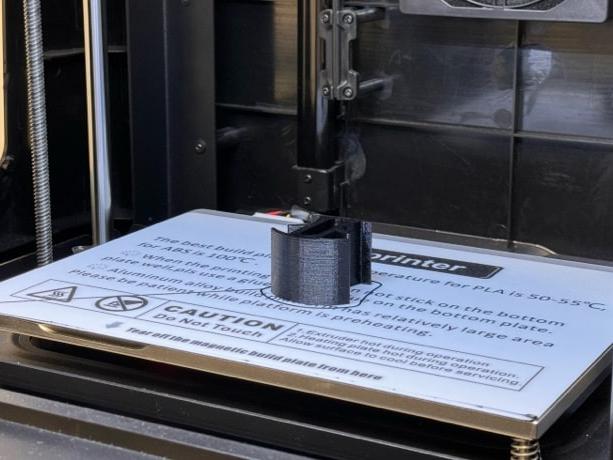
The technical team at Seals Direct helped work with this customer to develop a profile that could be inserted between these panels. This section had a central void that allowed the profile to compress when initially inserted into the gap. Once it place, the gap was large enough for the section to expand and adequately hold itself in the gap without the need for adhesive or mechanical fixings.
We decided to rapid prototype this section using our 3D printer and a flexible TPU filament. This allowed us to manufacture a short length within 2 hours of the design being approved by our customer. A number of test samples were then sent to the client for testing and evaluation. They concluded that they profile was suitable for the end application and instructed us to proceed with tooling to manufacture a significantly larger quantity in EPDM.
Prototyped seals have diverse applications across several industries. Rapid prototyping these seals with a flexible filament allows us to test our clients designs under various conditions to ensure optimal performance and durability before committing to full-scale production.
Rapid Prototyping with Seals Direct
The use of flexible 3D printer filament for rapid prototyping rubber seals offers numerous advantages, including flexibility, durability, chemical resistance and cost-effectiveness. By leveraging these benefits, we are able to accelerate our customers’ product development cycles, reduce costs and improve the overall quality of the final product. As 3D printing technology continues to evolve, flexible filaments will undoubtedly play an important role in the future of prototyping and manufacturing rubber seals.
At Seals Direct, our expert technical team has extensive experience in understanding our customers’ requirements and working together to identify a long-lasting sealing solutions. We can discuss the factors that influence the choice of rubber seal and explore custom rubber sealing solutions including rapid prototyping. Please contact us to discuss your requirements.