Seals Direct is a leading supplier of high-quality rubber seals, trims
and extrusions. The majority of our products are manufacturing through a process
called rubber extrusion.
We are proud to be one of the UK’s leading suppliers of rubber seals and trims
for the marine, industrial, caravan, automotive and film industries. Our team
are dedicated to providing the same high level of service, no matter whether
you require a few metres for a one off application or regular high volume production
runs. As well as stocking over 760 different products, we also design and
develop bespoke seals to our customers’ requirements. We are able to reverse
engineer products that are no longer available on the market.
In this article, we will explain how our products are manufactured and take a
detailed look into the complete rubber extrusion process.
What is Rubber Extrusion?
Rubber extrusion is a manufacturing process that is used to create rubber products such as seals, trims and tubing.
During the rubber extrusion process, natural or synthetic rubber is heated and pushed through a shaped die under high pressure. This forms a long continuous cross-sectional profile that can be coiled or cut to the desired length. Rubber extrusions can be produced in all manner of shapes and sizes, from simple profiles to more intricate custom sections.
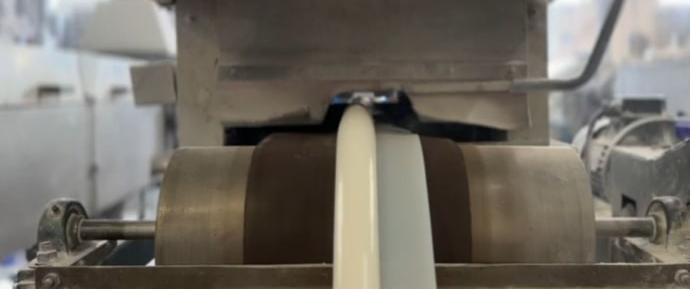
What Products Can be Made Using the Rubber Extrusion Process?
Rubber extrusion is a process that can be used to manufacture a wide variety of rubber products. Here are some products that are commonly produced using a rubber extruder.
- Rubber Seals: These products are used to effectively seal windows, doors and hatches against the ingress of air, water and dust.
- Rubber Trims: Trims provide a neat finish and effective protection for edges in a broad range of applications and industries. This includes automotive, furniture and construction.
- Weatherstripping: Often applied to windows and doors of buildings and vehicles to protect against the elements by sealing against air, water, and other debris.
- Automotive Components: Sealing automotive components includes bumpers and fenders that can be used to absorb impact and enhance the vehicle’s aesthetics.
- Tubing: Tube is used in the medical, automotive and industrial sectors to transport fluids and gases.
These extruded rubber products are widely used throughout many industries, including construction, industrial, automotive and healthcare.
What Are the Benefits of the Rubber Extrusion Process?
The rubber extrusion process is known in manufacturing for its efficiency and versatility. This offers several significant advantages.
Efficient and Cost-Effective Process
Rubber extrusion is a streamlined process that is capable of producing a high volume of products quickly at a low cost per part.
High Production Volumes
The extrusion process allows manufacturers to quickly produce a high volume of products, making it ideal for meeting large bulk orders and maintaining consistent supply chains.
Minimal Wastage
Because the extrusion process produces one continuous piece that can then be cut down to the required size, it is efficient at minimising material wastage, making the process more sustainable and increasing cost-efficiency.
Versatility
The process can be adapted to use various types of rubber, allowing manufacturers to produce products that are suitable for use in a wide range of environments and applications. Additionally, various dies can be used in the process to produce a wide variety of shapes and products, from simple tubing to more complex profiles.
What Equipment is Used in Rubber Extrusion?
Various specialist tools and machines are used to manufacture rubber
extrusions. In this section, we will explore some of the most important tools
and equipment used for manufacturing rubber products.
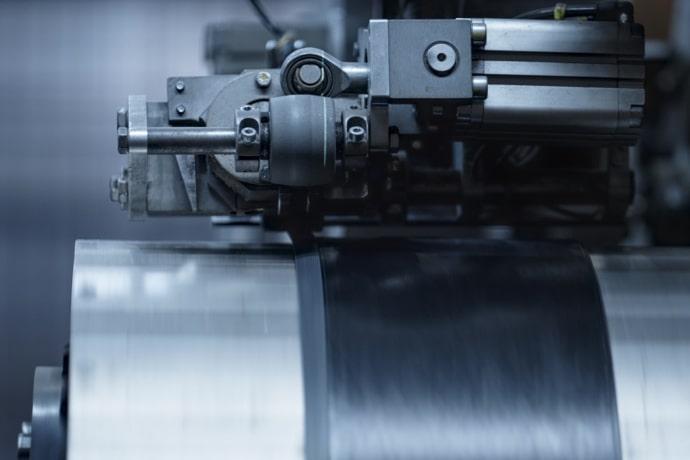
Natural or Synthetic Rubber Compound: Various types of rubber, including both natural and synthetic rubber, can be used to manufacture rubber extrusions. Synthetic rubbers popularly used during the extrusion process include EPDM, nitrile rubber (NBR), SBR and silicone.
Extruder for Rubber: The rubber extruder is the machine into which the rubber compound is fed to be heated and pushed through the die. The extruder consists of a barrel, a rotating screw and a drive mechanism.
Extrusion Eie: The die is the part that decides which type of product and shape is produced. Dies are usually custom-made to create a specific profile or shape.
Feeder: The feeder feeds the rubber compound into the extruder. The type of feeder used depends on the type of rubber being used.
Vulcanisation System: Once the rubber has been successfully
extruded, it may require vulcanisation, or curing to set the shape of the final
product.
Cooling System: After vulcanisation, the finished product needs to
be cooled to stabilise and solidify its shape. Depending on the type of rubber
being used, this is typically achieved using a water bath or air cooling
system.
Cutting Equipment: Finally, the continuous lengths of extruded
rubber are cut to size. The cutting tool required depends on what type of
product that is being cut. Guillotine cutters, straight-edge cutters, and tin
snips are all popular choices.
A Step-by-Step Guide to the Rubber Extrusion Process
The process may be slightly different depending on the material you are using and the product you are manufacturing. However, generally, the extrusion process can be split up into eight steps.
Step 1: Select and Prepare the Rubber Compound
Different types of rubber have different properties, making them suitable for different environments and applications. The first step in the process is to identify the most appropriate type of rubber for the product you wish to manufacture. Once you’ve selected your rubber, you may then blend it with additives to help achieve the desired properties.
Step 2: Feed the Rubber into the Extruder
Next, the rubber should be fed into the extruder. A strip feeder is usually used for solid rubbers, whilst a cold feeder is used for softer or more sensitive compounds.
Step 3: Extrusion
The rubber then passes through the extruder’s barrel, where it is heated to make it more pliable. The extruder contains a rotating screw within its barrel. The rotating screw applies heat, mixes and pressurises the rubber before pushing it towards the die.
Step 4: Shape the Product
As the temperature and pressure increase, the hot rubber is then forced through the die and shaped into the desired continuous profile or cross-section. It emerges from the die as a continuous length of profiled rubber.
Step 5: Vulcanisation (Curing)
Most extrusions need to be vulcanised immediately after extrusion to cure and harden the final product. Curing is usually achieved using a vulcanising chamber, where heat and sometimes pressure are used to vulcanise the rubber. There are various types of vulcanising machines, including hot air, steam and microwave machines. The process enhances the rubber’s strength, elasticity and durability. During vulcanisation, the rubber will usually shrink or swell.
Step 6: Cooling
After vulcanisation, the rubber products need to cool. This can either be achieved by turning down the temperature in the vulcanising chamber, by air cooling or in a water bath.
Step 7: Cutting
Once cooled, the extruded rubber can be removed from the cooling system using equipment like rollers or conveyors and cut to size using guillotine cutters or custom cutting equipment.
Step 8: Inspection
Finally, the products must be inspected for accuracy, surface quality and mechanical properties to ensure they meet the specified standards. Once approved, the products are packaged for shipment or moved to further processing or assembly stages.
Rubber Extrusion Industry Standards
When manufacturing products using a rubber extrusion process, certain industry standards must be complied with to ensure that the finished products are safe, consistent and fit for their intended purpose. These standards help manufacturers to ensure that they are working to high-quality standards. The specific standards and regulations that must be followed can vary depending on the products that are being manufactured and the industries that they are intended for. However, some of the key standards recognised in the manufacture of rubber extrusions include:
ISO 3302-1 Rubber Extrusion Tolerances
The international standard ISO 3302-1 specifies the tolerances on dimensions and irregularities of extruded rubber products. During the extrusion process, slight variations may occur from batch to batch. The standard ISO 3302-1 grades variations and sets out accepted tolerance levels. The three accepted levels are E1 (the tightest), E2 and E3 (the widest). All manufacturers should aim to exceed E1 where possible.
ISO 9001 Quality Management Systems
To comply with ISO 9001, the rubber extrusion manufacturer must demonstrate that it consistently provides products and services that meet customer, statutory, and regulatory requirements and that it aims to enhance customer satisfaction through the effective application of a quality management system.
ASTM Standards
The ASTM standards specific to rubber properties and testing methods, particularly ASTM D2000, require rubber manufacturers to examine and evaluate their material or product to ensure quality, safety, and resistance to various environmental factors.
Complying with these essential standards helps rubber extrusion manufacturers to ensure not only that they stay on the right side of the law but also that they are consistently manufacturing durable, safe, and high-performance products.
Rubber Extrusion Quality Control Measures
All rubber extrusion manufacturers must have strict quality control
measures in place to ensure that the products they produce comply with
regulatory standards and meet the required specifications and performance
criteria. These quality control measures should be implemented throughout each
step of the rubber extrusion process, from selecting the right material to
cutting the final product. Let’s take a look at some of the ways that quality
control is carried out throughout the rubber extrusion process.
Raw material inspection - The raw materials should be inspected for
purity and consistency before the extrusion process can begin.
Extruder monitoring - Once the rubber has been fed into the
extruder, the extruder’s temperature and pressure settings should be carefully
monitored, as any sudden changes could affect the finished product’s physical
properties.
Visual inspection – Measuring tools, like callipers and
micrometres, should be used to ensure that the extruded profile meets the
dimensional tolerances specified in the design. A visual inspection should also
be carried out to ensure that the surface is free from defects like cracks and
blisters.
Product testing – Finally, the finished product should be tested
for tensile strength, hardness, and resilience to ensure that it meets its
requirements and can maintain its properties under various conditions.
Documentation – Detailed records should be kept of all testing and
quality control results for traceability and quality audits. The results
obtained from quality control testing can also be used to refine and improve
processes and product quality over time.
Rubber Extrusions from Seals Direct
At Seals Direct, we are a leading supplier of rubber extrusions,
including different types of rubber seals, rubber U channels, rubber P seals,
rubber tadpole seals, T-shaped rubber seals, L-shaped rubber seals, and rubber
cords.
With over 50 years of experience, we can design and develop rubber extrusions
to meet any requirement. Whether you need one bespoke trim or a high volume of
extruded rubber products, our team are here to provide you with a fast,
efficient, and flexible service.
No job is too big or too small for our team. Our happy clients range from
individual customers to large-scale industrial enterprises, and we ensure that
every one of our customers receives the same high standard of service. Our huge
inventory includes over 760 different rubber products designed to meet various
requirements. And if we can’t solve your problem using one of those? Then we
can design and manufacture a bespoke solution just for you!
We attribute our success to our fast and efficient service and dedication to
solving every customer’s problem, no matter how big or small. Call our team
today at 01425
617722 for help or advice on selecting the right rubber
extrusion to meet your requirements.