Large ships and marine vessels such as oil tankers and cruise liners are fitted with watertight doors, hatches and skylights which are used to isolate sections of the ship in the event of flooding, fire and smoke. These doors are often fitted with multiple latching points so need a heavy duty and long lasting seal to stop water ingress.
Watertight door and hatch seals are manufactured with a sponge core bonded to a solid rubber outer skin. This outer shell helps strengthen the seal when closed whilst the internal sponge allows for easy compression. This combination creates a long lasting, heavy duty seal which helps maintain a reliable watertight environment. These seals are manufactured with two chamfered corners to allow the seal to security fit into the channel to allow for the weld fillets.
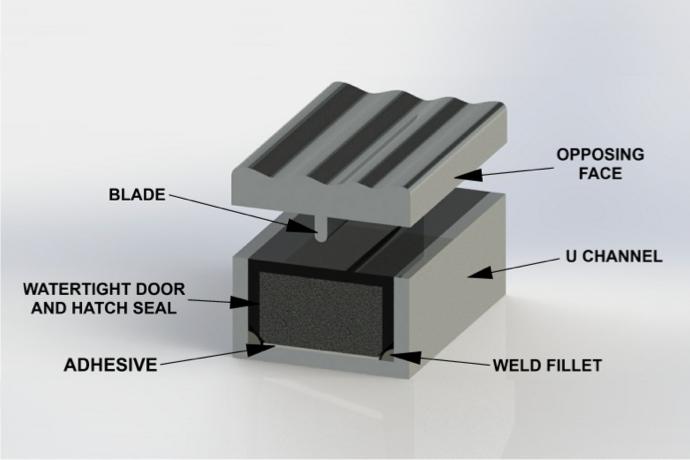
These seals are fitted into a metal channel attached to either the door / hatch or surrounding frame. This channel is typically manufactured by welding sheets of metal together to form a ‘U’ shape. The seal should be bonded into the channel using a suitable adhesive, such as a Polyurethane or contact adhesive. If using a contact adhesive, you should only apply the adhesive to the bottom of the channel to prevent the seal from sticking on the sides during installation.
The opposing face should be fitted with a round ended blade which will insert into the seal as the door / hatch closes. Typical compression of the seal should be between 3mm and 5mm although this can be varied by experimentation should the need arise. Take care not to over compress the seal as this will cause compression set damaging the recovery of the seal.
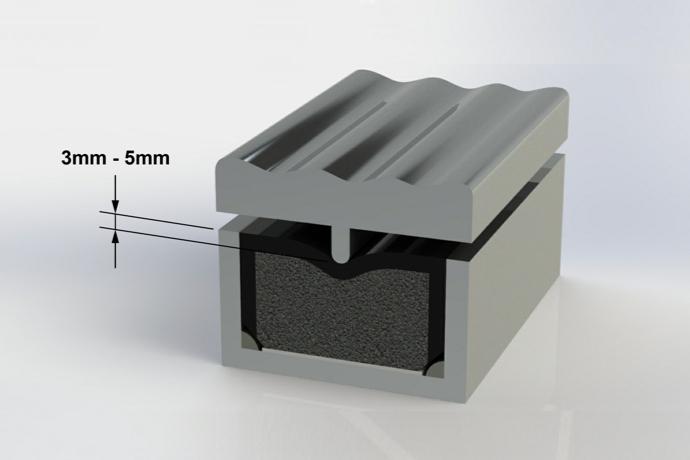
These seals are fitted into a metal channel attached to either the door / hatch or surrounding frame. This channel is typically manufactured by welding sheets of metal together to form a ‘U’ shape. The seal should be bonded into the channel using a suitable adhesive, such as a Polyurethane or contact adhesive. If using a contact adhesive, you should only apply the adhesive to the bottom of the channel to prevent the seal from sticking on the sides during installation.
The opposing face should be fitted with a round ended blade which will insert into the seal as the door / hatch closes. Typical compression of the seal should be between 3mm and 5mm although this can be varied by experimentation should the need arise. Take care not to over compress the seal as this will cause compression set damaging the recovery of the seal.