Rubber seals play an essential role in various sealing applications. They act as a barrier protecting your boat, car, van or home from air leaks and water ingress. Despite their versatility and durability, rubber seals can deteriorate, crack or split, increasing the chance of failure and damage to your property. The deterioration of rubber seals is a multifaceted issue influenced by environmental, chemical and mechanical factors. Understanding what causes this degradation and how to prevent it is essential for maintaining the integrity and functionality of your rubber sections.
Why Does Rubber Deteriorate?
Environmental Factors
One of the primary reasons for the degradation of rubber is the exposure to environmental elements. Sunlight, particularly its ultraviolet rays, can have a detrimental effect on rubber, causing it to harden, crack and lose its elasticity. This process, known as photo-degradation, occurs when the UV rays break down the chemical bonds within the rubber. This is especially problematic for rubber seals used outdoors, such as in vehicles, boats or exterior machinery, where they are constantly exposed to sunlight.
Temperature extremes also play a significant role in rubber deterioration. High temperatures can cause the rubber to soften and lose its shape, impairing its sealing capability. Over time this exposure can lead to thermal degradation, where the rubbers molecular structure breaks down. Conversely, exposure to low temperatures can make rubber brittle and prone to cracking. The temperature-induced wear is a particular concern in environments with wide temperature fluctuations, such as automotive engines or refrigeration systems.
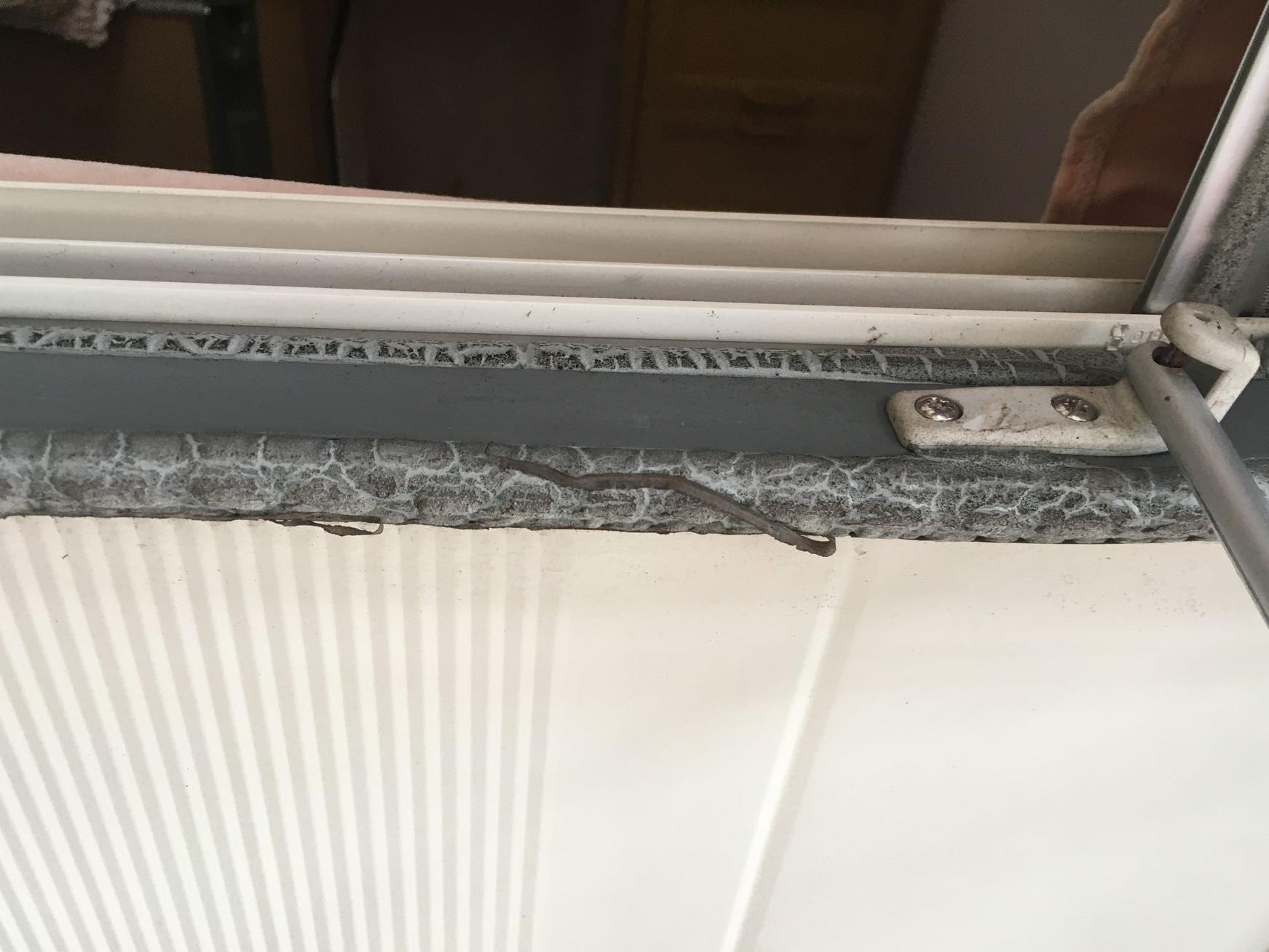
Chemical Factors
Rubber seals often come into contact with various chemicals, which can accelerate their degradation. Oils, solvents, acids and other harsh substances can cause the rubber to swell, soften or even break down entirely. This chemical attack depends largely on the rubbers composition and the nature of the chemical. For example, some rubber types, such as nitrile, are more resistant to oil and fuel, making them suitable for use automotive applications, where they are likely to come into contact with these substances.
Ozone and Oxygen Exposure
Ozone and oxygen exposure can also significantly impact the integrity of rubber seals. Ozone, a reactive form of oxygen present in the atmosphere, can cause rubber to crack on the surface. Even small amounts of ozone can create deep cracks when the rubber is under prolonged and excessive tension. Oxygen can lead to the oxidation of rubber, a process that results in its hardening and loss of elasticity. This oxidation process is gradual but can be accelerated by higher temperatures and the presence of UV light.
Mechanical Stress
Mechanical factors, including compression, stretching and abrasion can cause the physical deterioration of rubber seals. In applications where seals are under constant pressure or movement, such as in pumps or rotating shafts, the rubber can wear out, leading to tears, breaks or a general decrease in its sealing effectiveness. The extent of this wear often depends on the nature of the application and the rubbers quality and design.
How Can I Prevent Rubber Seals Deteriorating?
Preventing the degradation of rubber is essential for maintaining its integrity and functionality. Understanding how you can prevent rubber degrading will help extend the life of your rubber seals, requiring fewer replacements and reducing the chance of damage.
Material Selection
The choice of rubber material is paramount in preventing degradation. Different types of rubber have varying resistances to environmental and chemical stresses. For example, silicone rubber is highly resistant to temperature extremes, making it ideal for outdoor applications. Nitrile rubber, on the other hand, is resistant to oils and is often used in automotive applications. Selecting the right type of rubber for the specific conditions it will face can significantly extend the life of a seal.
Proper Installation and Maintenance
Correctly installing the rubber seal is essential for preventing mechanical stress-related degradation. Over-tightening or improper fitting can cause excessive stress and early failure, requiring more frequent replacements and potential damage to other components. In dynamic applications, lubricating the surface can reduce friction and wear. The type of lubricant used should be compatible with the rubber material to avoid chemical degradation but silicone-based lubricants are generally safe for a wide range of rubber types.
Regular inspections and testing can help identify problems early, allowing for timely interventions. Having a schedule for routine replacement based on the seals expected lifespan and the conditions it is exposed to can also help prevent early failure. Regular maintenance should include periodic inspections for signs of wear and tear and the timely cleaning of harmful substances can help extend the lifespan and efficiency of the seal.
Protective Coatings and Additives
Applying protective coatings to rubber seals can provide an additional barrier against environmental factors. UV-resistant coatings can protect against sunlight degradation, while other coatings can increase resistance to chemicals or ozone. Additives can also be mixed into the rubber compound to enhance certain properties. For instance, antioxidants and antiozonants can be added to prevent oxidation and ozone cracking.
Design Considerations
The design of the seal and the system it is used in can greatly impact its lifespan. Proper sizing and fitting ensure that the seal is not over-compressed or stretched beyond its capacity. The shape of the seal can also influence its durability; for instance, rounded corners are less likely to develop cracks than sharp edges. In dynamic systems, where seals are in constant motion, designing for minimal friction and wear can prevent premature degradation.
Environmental Control
Controlling the environment in which the rubber seals are used can significantly reduce the risk of degradation. This includes shielding the seals from direct sunlight to prevent UV damage and maintaining a stable temperature to avoid the harm of thermal degradation. In industrial settings, reducing exposure to harmful chemicals or selecting less aggressive alternatives can also prolong the life of your section.
Quality Assurance
Investing in high-quality rubber seals can also prevent premature degradation. Higher quality materials are generally more resistant to environmental and chemical stresses and are less likely to have manufacturing defects that can lead to early failure. Working with reputable manufacturers and suppliers, such as Seals Direct, ensures that the seals meet the necessary standards and specifications for the intended application.
At Seals Direct we manufacture all of our products from high-quality rubber compounds that do not include excessive amounts of filler or recycled rubber. All of our moulded and extruded rubber products are stored in a cool, dry place away from direct sunlight and ozone sources.
Training and Awareness
Ensuring that personnel who handle and install rubber seals are properly trained can significantly reduce the risk of premature degradation. Training should cover the correct installation techniques, understanding the importance of environmental factors, and how to identify signs of wear and tear.
What Is the Shelf Life of Rubber?
The shelf life of a rubber seal or gasket varies depending on several factors, including the type of rubber, the conditions under which it's stored and the specific formulation of the rubber compound. As a general rule, the shelf life for many rubber-related products is often considered to be around 5 to 10 years, if properly stored and maintained. However, this is a very rough estimate and can vary widely.
The expected shelf life of a rubber seal manufactured from different rubber compounds is detailed below.
Rubber Material Compound
Expected Shelf Life
3 to 5 Years
3 to 5 Years
5 to 10 Years
5 to 10 Years
5 to 10 Years
20 Years
20 Years
Typically, products manufactured from materials such as Silicone and Viton will last much longer than rubber seals manufactured from other compounds. Although these materials are associated with higher initial manufacturing costs they may be cheaper in the long term due to less frequent replacements.
At Seals Direct, our expert team has extensive experience in understanding our customers’ requirements and recommending the best type of rubber for your application. We can discuss the factors that influence the choice of rubber seal and explore custom rubber sealing solutions or off-the-shelf products. Please contact us to discuss your requirements.