A Complete Guide to SBR Rubber
What is SBR Rubber?
SBR, also known as styrene-butadiene rubber, is a general purpose synthetic rubber that offers a cost effective alternative to natural rubber (NR). Although SBR shares most of the same characteristics as natural rubber, it is manufactured from petroleum by-products rather than latex sap. Styrene-butadiene rubber has a diverse range of properties including good abrasion resistance and high tensile strength that makes it suitable for the production of tyres, conveyor belts and various rubber sealing products. With an annual production that exceeds 5 to 6 million metric tons, SBR is used in a large range of projects within most industry sectors.
This guide provides a detailed background to the history and production of SBR rubber. It also explains the advantages and disadvantages of using this material in the production of custom rubber products and gaskets.
How is SBR Rubber Made?
The history of styrene-butadiene rubber dates back to the early 20th century and is closely tied to the developments of the synthetic rubber industry. In the early 1900s the demand for rubber was growing rapidly and natural rubber, the only rubber available at this time, was in short supply and subject to significant fluctuations in price. The invention of SBR occurred between 1910 and 1930 where chemists at Notre Dame University built on the previous work of a German chemist and successfully polymerised butadiene and styrene. This created what became styrene-butadiene rubber which was commercialised and sold as the first synthetic rubber compound.
SBR is a synthetic rubber polymer made through a process called emulsion polymerisation. This process involves mixing two monomers (styrene and butadiene) with water and emulsifying agents, then initiating a polymerisation reaction using heat and a chemical initiator. The rubber compound is made up of 75% butadiene and 25% styrene and can be used to manufacture bespoke extrusions, or flat sheets and strips of rubber.
Manufacturing a rubber seal in SBR can be achieved by pushing the rubber compound through an extrusion tool (known as a die) on an industrial extruder. This machine uses pressure and temperature to extrude the required shape, as determined by the hole in the die. The extruded section is then cured and hardened using a vulcanising line, steam line, salt bath or autoclave cure depending on the size of the section and overall length. Styrene-butadiene rubber can also be turned into flat sheets by rolling the compound using a calender roller to a required thickness. This process creates large sheets that can be cut into narrow strips for other applications.
Most synthetic rubbers are available in solid and closed-cell sponge variants. However, styrene-butadiene rubber is only available as a solid rubber in a limited range of hardnesses.
Advantages of SBR Rubber
Styrene-butadiene rubber is low-cost material that offers several advantages that make it a popular choice for rubber seals, sheet and gaskets. It exhibits a good abrasion resistance and tensile strength so is often the material of choice for applications that require a synthetic alternative to natural rubber. Some of the main advantages and characteristics of SBR rubber include;
- Abrasion
Resistance: Although natural rubber demonstrates better abrasion
resistance, styrene-butadiene rubber exhibits excellent resistance compared
to other synthetic compounds. This makes seals manufactured from SBR highly
durable and suitable for applications subjected to wear and friction, such as
tyres and conveyor belts.
- Tensile
Strength: One of the most desirable characteristics of SBR is its tensile
strength. This creates a resilient material that can withstand large stretching
forces without breaking or permanently deforming. It is also highly flexible so
can be bent or twisted without cracking or splitting.
- Cost-Effective:
SBR is relatively inexpensive to produce compared to natural rubber and
other synthetic rubber compounds. The raw materials, styrene and butadiene, are
derived from petrochemical sources that are readily available in large quantities.
The production process is also relatively simple and suitable for large scale
production. This cost benefit allows SBR to be blended with other rubber
compounds, such as Nitrile, to create a low-cost product with improved resistance
properties.
- UV and
Ozone Resistance: Whilst SBR does not have good resistance to UV and
ozone, it performs slightly better than natural rubber when exposed to
sunlight. This makes it suitable for applications that require a high
elasticity material that will experience some exposure to UV and ozone.
However, it is often better to consider alternative materials with better UV
stability for instances where the sealing solution will encounter prolonged exposure
to sunlight.
- Chemical Resistance: Whilst SBR is not as chemically resistant as some other synthetic rubbers, such as EPDM, it offers moderate resistance to a variety of chemicals and cleaning fluids.
Disadvantages of SBR Rubber
Although styrene-butadiene rubber offers a number of advantages, such as its abrasion resistance, compression recovery and tensile strength, its suitability for a particular application depends on the specific requirements and conditions. There are occasions where natural rubber or other synthetic rubber compounds would be better suited. Some of the disadvantages of using SBR rubber include;
- Sensitivity
to Temperatures: The typical working temperature for SBR rubber is -25°C to
100°C, which is a slight improvement on the -20°C to 70°C temperature
resistance of natural rubber. However, unless a material with superior tensile
strength and compression recovery is essential, this temperature range may be a
limiting factor in some sealing solutions. It may not be suitable for
high-temperature applications as it can soften or degrade at elevated temperatures.
- Poor
Weather Resistance: Although SBR is considered better than natural rubber
for outdoor applications, it is significantly less resistant to weathering and
UV radiation than other synthetic rubber compounds. Styrene-butadiene rubber
may experience degradation, cracking or colour fading over extended periods.
- Age Hardens: SBR rubber can harden and lose its flexibility over time, especially when exposed to heat and oxygen. This aging process can affect its long-term performance and characteristics such as its tensile strength.
Types and Grades of SBR Rubber
SBR is available in a small selection of grades suitable for different projects. As a material that can be extruded or cut from large sheets, styrene-butadiene rubber provides a solution to most applications that are looking for a low-cost sealing product. The formulation of SBR can vary, so selecting the correct grade is essential for ensuring optimal performance.
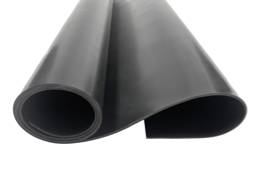
Commercial Grade SBR Rubber
Commercial
grade SBR rubber is a cost efficient general purpose product that provides a
sealing solution where a cheaper quality material will suit. It can be
manufactured at a lower cost than premium grades and other synthetic rubber
compounds as it contains a high percentage of fillers, such as carbon black and
talc. These reduce the overall percentage of rubber which may affect its
mechanical properties.
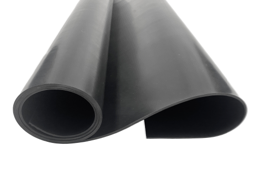
Premium Grade SBR Rubber
Premium
grade styrene-butadiene rubber contains a higher concentration of rubber than commercial
grades. This helps increase the compounds characteristics such as its compression
recovery, tensile strength and UV stability. It is with a hardness of around 50°sh
A.
Contact Us
With more than 50 years' experience in the rubber sealing industry, our expert team has extensive experience in finding sealing solutions for our customers. Contact our technical experts via phone or email for sealing advice or custom quotations.